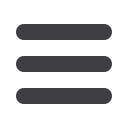

Thermal imaging camera can avert disaster
The Land Arc range of cameras are general purpose radiometric thermal imaging cameras
which are designed to be rugged enough for industrial applications while being small enough
to fit into confined areas. Introduced locally by
Protea Automation
, the cameras are used to
detect hot spots that are above the desired temperature of materials being transported.With
parameters stored onboard the camera as well as on the Arc Land Imaging Processing Soft-
ware (LIPS), the detection of a hotspot will trigger an alarm and set in motion a sequence of
measures to prevent fire and avoid damage to the belt. In the event of the SCADA or control
system being unavailable, the onboard intelligence of the camera acts as a failsafe system
and still triggers an alarm that will allow appropriate action to be taken. “Management of
warm materials on conveyors is a hot topic following a recent fire which destroyed an entire
incline conveyor system at a lime manufacturing plant in the Northern Cape which caused
millions of Rands' damage to the plant and led to considerable loss of production,” says Gavin.
“Following the catastrophe we were called in to design and install a system to prevent a
recurrence of this type of event and have subsequently installed Land ArcThermal cameras
as well as scanners to identify hotspots, as well as identify trends which show when the
temperature of clinker from the rotary kilns is rising above the normal range.With the equip-
ment and procedures in place the plant is now able to significantly reduce costly belt repairs,
reduce downtime and prevent dangerous situations from occurring in future.”
Enquiries: GavinWestley. Email:
gavinw@protea.co.zaTakes less space in the control cabinet
Due to innovative technologies, the newAS-i power supplies from
ifm electronic
require con-
siderably less space in the control cabinet, as compared to common cabinet power supplies.
Another advantage of the efficient design is the above average degree of efficiency of up to
94%. This saves energy costs and reduces waste heat in the control cabinet. The switched-
mode power supplies provide the specific nominal power across the entire temperature
range. Derating only has to be taken into account above an operating temperature of 60 °C.
All AS-i switched-mode power supplies are equipped with double terminals.This simpli-
fies wiring and provides more clarity in the control cabinet. Instead of an inrush current
limitation with a simple NTC, charging the capacitors of the switched-mode power supplies
is microprocessor-controlled.This ensures an ideal start-up of the voltage supply. In the de-
velopment of the power supplies, particular
importance was attached to the dimension-
ing of the components, so that operation
is permanently ensured. This results in an
excellent MTBF value of about 1,4 million
hours. Moreover, all ifm power supplies
feature sufficient power reserves to reliably
handle even short current spikes.
Enquiries:Tel. 012 450 0370 or
SIL2-certified wireless
gas detection system for
LNG facility
Yokogawa
and
GasSecure AS
, a Dräger
owned company, have produced the
world’s first SIL2-certified wireless gas de-
tection system for use at an LNG facility in
Northern Europe. Yokogawa has been de-
veloping a wide variety of ISA100 wireless
technologies and field wireless devices
such as adapters that enable conventional
wired devices to access wireless networks.
Yokogawa supplies these technologies and
devices to plants and other facilities pri-
marily in the upstream oil and gas sector.
GasSecure has developed ISA100 Wire-
less gas detectors that can detect leaks
of explosive hydrocarbon gases and are
certified for compliance with the ATEX di-
rective and the IEC Ex Certified Equipment
Scheme. The gas detectors are installed
on offshore oil and gas drilling platforms
and at tank farms, industrial plants, and
the like. GasSecure has already supplied
a number of these products to leading
oil and gas companies around the world.
In 2014, GasSecure and
Yokogawa
con-
cluded an agreement under which the two
companies jointly developed a wireless
gas detection system that wouldmeet their
customers’ requirements.
This system uses GasSecure’s GS01
wireless gas detectors to measure hy-
drocarbon gas concentrations. Using
the ISA100 Wireless communications
protocol, the GS01 establishes a link with
a Yokogawa YFGW510 access point and
sends data to a host systemvia aYokogawa
YFGW410 field wireless management
station. Although the GS01 uses a low-
power infrared sensor and is very energy
efficient, it has a very fast response time.
This capability of the GS01 and the utilisa-
tion of dual redundant communications
by Yokogawa’s field wireless products
make them essential components for the
construction of a fast and highly reliable
monitoring solution. To meet its custom-
ers’ safety requirements, GasSecure has
made enhancements to the GS01 to obtain
SIL2 certification for this device. For its
part,Yokogawa has modified theYFGW410
so that it now supports the PROFIsafe
safety communication standard, and has
verified that both companies’ products
perform and operate as specified.
Enquiries: Christie Cronje.Tel. 11 831 6300
or email
Christie.cronje@za.yokogawa.comROUND UP
CONTROL SYSTEMS + AUTOMATION
Electricity+Control
September ‘15
14