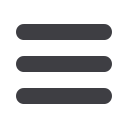

News
Technology
January 2013
33
www.read-eurowire.comEnergy savings, reduction of emissions and cost savings
are important selling points in all sectors of the steel and
non-ferrous industry. The hydraulic system also offers great
potential here. A new technical solution from SMS Meer provides
considerable advantages.
The variable speed pump, VSP for short, enables an efficient
hydraulic system with pressures of more than 450 bar.
The two major Russian pipe producers, Vyksa Steelworks (OMK)
and Izhorsky Trubny Zavod (Severstal), will soon be using the
VSP technology on two pipe closure presses (each with 25 MN
pressing force and four pressing cylinders).
The general principle is that the oil pressure is generated only on
the system level – meaning only when it is actually required.
Commercially available axial piston pumps are used, and regulation
follows through the speed of the servomotors. With energy
efficiency and environmental compatibility, this technology fulfils
the guidelines of the SMS Meer‘Ecoplants’systems.
Set-up is performed using proportional valve technology,
during which the complete throttling of the hydraulic power by
significantly heating up of the oil is completely eliminated.
As a result, an extremely energy-saving and low-loss hydraulic
system is built up with the ‘small’ systems, but also with high
pressing forces as well as with several hydraulic axles.
Only the oil pressure and volumetric flow that are actually
required by the system are generated.
In this respect, the motors only run during the main machine
function (eg pressing process), but are idle in the non-productive
time.
This means less power consumption and lower noise burden.
The structure also enables feedback into the power network,
something like that from the compression energy of the oil.
Hydraulic systems with VSP require neither a cooling system nor
a central hydraulic station with a large tank.
The costs of housings or hydraulic pits as well as long pipelines
are eliminated. All hydraulic components are mounted directly in
an easy-to-maintain way or on top of the machine.
Longer lifetime of the oil also make a contribution towards the
low repair costs as do the low number of wearing parts and the
modular, easily exchangeable components.
The integrated control of the pump parameters even allows
preventive repair and maintenance. This means that it can be
seen if a component should be replaced in the near future.
SMS Meer GmbH – Germany
Website
:
www.sms-meer.comNew technology achieves high-energy savings
Metalube launched a semi-synthetic
oil, Inoxol™ 5108, at Wire & Cable India
2012. This latest addition to its lubricant
range is specifically designed for the
wet drawing of stainless steel wire and
significantly outperforms rival products.
Inoxol™ 5108 contains the very latest
synthetic additives, improving film
strength and providing outstanding
extreme-pressure
and
anti-wear
properties.
Technical
director
Chris
Nettleship
said: “Our test results for this product
are exceptional. We are witnessing
excellent drawing performance that will
considerably extend the life of dies, and
as the cost of dies is noticeably higher
than that of a lubricant, the results speak
for themselves. Inoxol™ 5108 will radically
reduce customer overheads.”
Inoxol™ 5108 also contains special
additives to minimise thermal and
oxidative degradation of the oil,
extending the service life of the oil,
reducing both the quantity of oil
consumed as well as the cost of waste
oil disposal. The improved lubricity
benefits provided by these additives
also produce an exceptionally bright
surface finish.
Laboratory wear tests have shown that
Inoxol 598 reduces wear by more than
20% compared to its nearest rival.
Metalube specialises in wire and tube
drawing lubricants, working with wire,
cabling
and
tubing
manufacturers
across the world. The headquarters
are in Manchester, UK, where the site
incorporates offices with warehousing,
laboratories and manufacturing facilities.
Metalube – UK
Website
:
www.metalube.co.ukNew lubricants India launch
▲
▲
Albert Malloy, general manager Metalube; Joseph
Ellingworth, Metalube India and Amit Gupte,
general manager Metalube India pictured at Wire
and Cable India