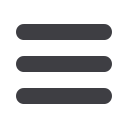

Feature
Testing & measuring
January 2013
38
www.read-eurowire.comWire surface detector
Italy-based Rigon Instruments has launched
a compact in-line rectangular or round
enamelled wire surface detector tester,
model WSD, capable of detecting blisters and
lumps, in compliance with the most stringent
international standard.
The company claims that the digital contact
technology used for the measurement,
compared to the analogue technology already
present in the market, ensures long-term
stability, repeatability and electrical noise
immunity, suitable for working in harsh
environments requiring at the same time
low maintenance. Its design allows an easy
threading in very small area, avoiding bend
and stress of enamelled wire. The device can be
positioned in different ways without measuring
problems.
The blister detector is a modular system that can be assembled to control two or all four surfaces of strip wire, with the possibility
to install a soft conductive electrode to perform high voltage continuity of covering test up to 3,000 Vdc, under the supervision of
dedicated software, which allows the setting of minimum detectable blister, test voltage and current, pre-alarm and alarm for each
test length, with a final customisable report for each reel produced.
Rigon Instruments – Italy
Website
:
www.rigon.it▲
▲
Model WSD - digital compact technology
The CAPRIS® CMS2 (‘Contrast Measurement
System 2’) is a patented system, specifically
designed for off-line contrast measurement
of laser generated marks on electrical
wiring and fibre optic cabling employed in
aerospace and other critical industries. It
provides a convenient quality assurance tool
that can be employed simply and quickly
to monitor and measure the average
contrast of user applied and/or manufacturer
markings on wire and cable.
The CMS2 uses optical technology to
calculate the contrast by measuring the
variation in luminance on the surface of a
sample over an area encompassing the mark
and the unmarked insulation.
This type of measurement is a key
requirement for a number of aerospace
customers and end users such as Boeing,
Airbus, Sikorsky and the US Navy, to ensure
the quality and legibility of marks on their
wire.
Generally anything giving less than a 40 per cent contrast is unacceptable. Spectrum Technologies brought the first CMS system
to market in 1996 and since then many modifications have been made to make the technology faster, smaller, cheaper and more
accurate. In particular, following a two-year US Navy-funded project, the US National Institute of Standards & Technology (NIST)
verified the operation and performance of the CAPRIS CMS2.
As part of the project, the measurement algorithm was enhanced to improve performance on coloured wires, lower contrast
values and smaller marks, as well as confirming the accuracy on white wires of ±2% and the repeatability of the system of ±1%.
The CAPRIS CMS2 has since been qualified to Boeing and Sikorsky specifications BAC 5152 and SS7333, respectively, as well as
complying with other international aerospace standards.
SpectrumTechnologies Plc
– UK
Website
:
www.spectrumtech.com▲
▲
The CAPRIS® CMS2 from Spectrum Technologies
Patented off-line system