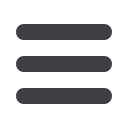

Technical article
September 2012
69
www.read-eurowire.comTechnical requirements
and problems caused
by wire geometry and
processing
Colour measurement on the base of
CIE-Lab is today state-of-the-art in the
paint industry or graphic art applications,
with tolerance values of sometimes
∆
E < 1.
Conditions for such exact measurements
are plane objects, a scan spot with
a diameter of some 5-10mm and a
sampling time in the order of 100ms
on a motionless object – but all these
conditions are definitely not given at an
extrusion line.
That’s why an inline measurement has to
consider the following points:
• With a very short sampling time an
averaging over a certain number of
single shots eliminates local devia-
tions. This is justifiable, as colour
changes in extrusion have a relatively
long transition time caused by mixing
effects in the barrel
• Object movement (jitter) has to be
minimised at the sensor position. This
is important for the object-sensor
distance d
s
(illumination reduces
with d
s
2
) as well as for transversal
movement, where the object is leaving
the scan spot partially or completely
• The wire geometry is detected as
a side view on a cylinder surface.
This results in a colour variation
from the cylinder centre view towards
the cylinder border. This effect is
also influenced by the surface
roughness.
As both conditions cannot be
changed, the final colour value
cannot be interpreted as an absolute
measurement
but
as
relative
measurement with high reproducibility
Normally
one
line
runs
different
conductor/insulation
diameters.
The
device should be able to work with
various geometries (over a certain
range) without mechanical preparation or
sensor recalibration.
One more challenge is the measurement
in a production of colour-coded wires (one
or two stripes).
As the final colour establishes after
the cooling down of the polymer,
sampling has to be done behind the
cooling trough.
Caused by redirecting wheels and
the product itself (particularly stranded
conductor), the wire can turn around
the longitudinal axis in an irregular way.
Therefore the sensor detects sometimes
the main colour, sometimes the stripe
colour, or both at the same time in the
scan field.
Figure 3
gives an impression of the sensor’s
view on a two-coloured wire.
With sophisticated mechanics the wire
turning can be changed to be more
regular and used for main and stripe
colour detection with only one sensor.
▲
▲
Figure 5
:
Left side –
∆
E calculated from data in picture 4 (with setpoints 87.62/-66.04/39.10)
Right side
–
Histogram of
∆
E with a binning of 0.05. Average
∆
E = 0.89
▲
▲
Figure 6
:
Forced colour fault by putting blue masterbatch into the barrel feeding
▼
▼
Figure 7
:
Raw data with stripe – well recognisable changes in a*- and b*-channel when the stripe is moving
through the scan field
1.Col. Test (Yellow) 2011-04-28
distribution of
d
E (binning = 0.05)
sampling time [min]
d
E [AU]
d
E [AU]
Dual colour test (blue-green)
raw signal L*, a*, b* [AU]
test length [AU]
Yellow insulated cable with masterbatch fault from hopper (blue grain)
Time [min]
d
E [L*a*b*]