
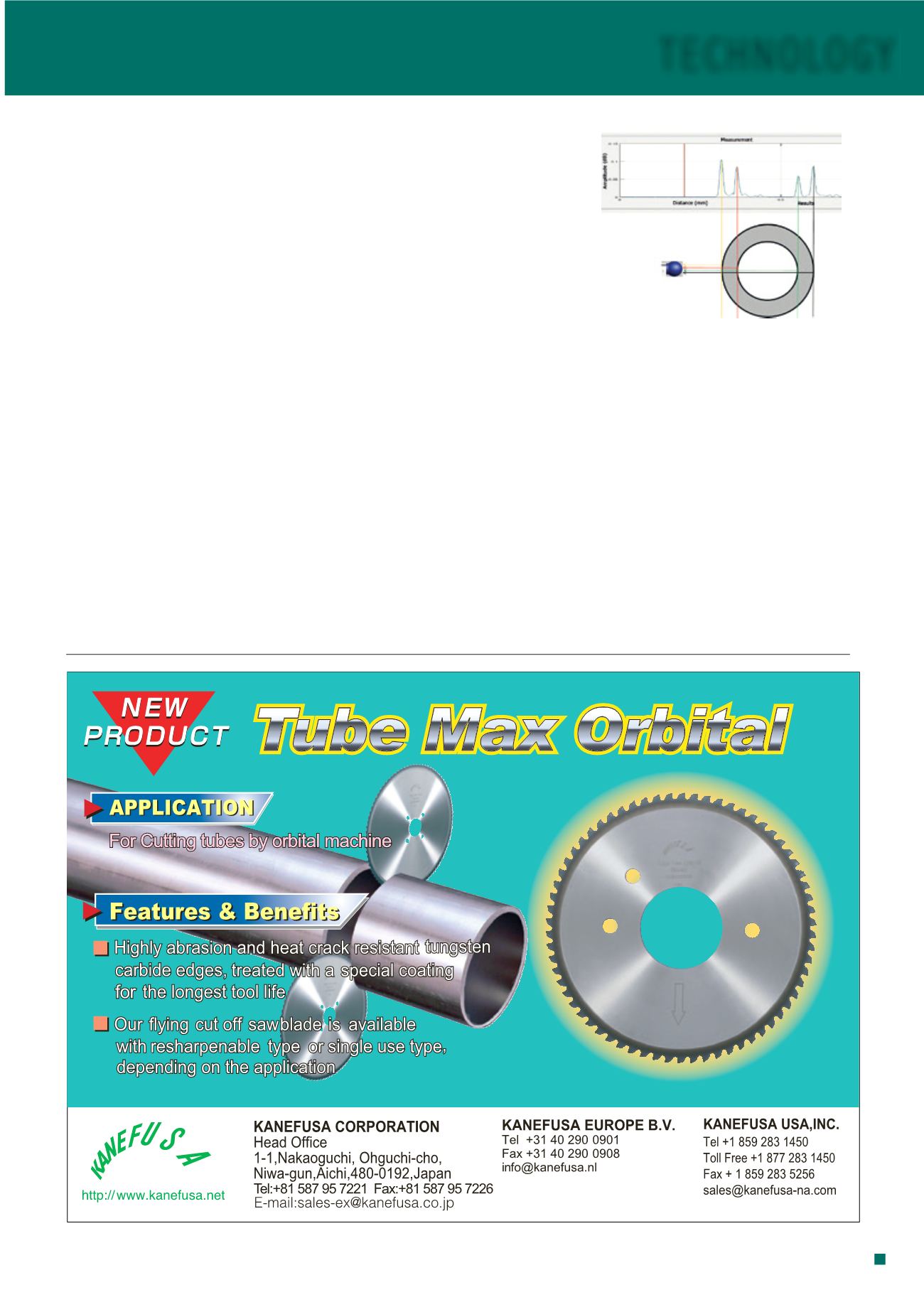
J
uly
2016
47
T E CHNOLOG Y
a special challenge. As a result of the
temperature dependence of ultrasonic,
a temperature compensation is required.
But the goal is to achieve, as early as
possible in the production process,
reliable and precise information about
tube dimensions in order to take action if
necessary and to avoid failure deliveries.
Moreover, it is necessary to approach
early in the production process the
minimum permissible tube dimensions to
produce a minimum metre weight. Cost
savings resulting from the low metre
weight are often decisive in competition.
Material costs of extruded plastic tubes
account for up to 90 per cent of the total
manufacturing costs.
Depending on throughput of the line,
used material type and underlying norm,
between the minimum and maximum
permissible tube dimensions there is an
annual savings potential in the single-digit
millions range. In addition, the production
of standardised plastic tubes assures
a flawless processing of the tubes. For
example, quality tubes can be welded
easily. Thus, the use of a millimetre wave
measuring system leads to significant
time and material savings, as well as to a
high quality end product.
Areas of application of technology
The millimetre wave technology is
suitable for the measurement of any kind
of plastic tubes with a diameter from 120
to 2,500mm that are, for example, used
for conducting water, gas, chemicals
and oil. Particularly interesting is the
application of tubes made of all common
plastics, such as PE, HDPE, PP, PA6,
PVC, etc. Here the system provides
precise measuring values, even for tubes
with wall thicknesses of 200mm.
Another area of application is the
measurement of single- and multi-layer
tubes. During production, there is the
risk that the melt that leaves the tube
tool flows down as a result of gravity
and thus negatively influences the tube
wall thickness distribution. This so-called
sagging is identified by the millimetre
wave measuring method.
Conclusion and outlook
Quality demands when manufacturing
large plastic tubes are increasing. Norms
precisely define the dimensions of the
products to be produced. The precise and
reliable quality assurance of plastic tubes
during extrusion is gaining importance.
By the use of a new system on the basis
of millimetre wave technology for hot
measurement and at the cold measuring
end for final quality control, the product
parameters of inner and outer diameter,
ovality, wall thickness and sagging are
continuously monitored online.
The introduced millimetre wave
technology, in combination with processor
systems, increases quality, minimises
material consumption, and contributes to
time and cost saving.
Sikora AG
– Germany
Email:
sales@sikora.netWebsite:
www.sikora.netEvaluation of the received signals and
determination of the tube dimensions