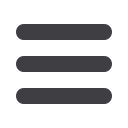

28
CONSTRUCTION WORLD
FEBRUARY
2016
PROJECTS AND CONTRACTS
The foundations are designed using
an 89% replacement of cement,
resulting in, what we believe to be,
one of the world’s lowest carbon
footprints for any wind farm foundation;
according to research scientist, and head of
Murray & Roberts’ Concrete Centre for Excel-
lence, Cyril Attwell.
The first two bases, which were
completed on 13 October, utilised an 80%
replacement of Portland cement, while the
remaining foundations use a unique design
comprising 35 kg of high grade Portland
cement per cubic metre, an 89% reduction
from a standard concrete mix. This compo-
sition has resulted in the wind farm’s carbon
footprint being reduced to approximately
90,7 kg of carbon dioxide per cubic metre.
Ground Granulated Corex Slag (GGCS), a
by-product from the iron industry, is used to
replace 89% of the cement.
“Cement manufacturing is typically a
highly energy intensive process. By substi-
tuting the cement with a by-product such as
GGCS, we are able to reduce our carbon foot-
print considerably,” said Leo Quinn, project
manager for Loeriesfontein Wind Farm.
A 28-day compressive strength test has
been completed, which indicated that the
80% replacement ratio achieved an impres-
sive strength of 55 MPa (megapascals), and an
expected ultimate strength of 100 MPa, within
a 56 day period. “The strength of concrete is
measured in megapascals; theoretically
a cubic metre of concrete that is rated
30 MPa, is able to withstand the weight of
six bull elephants, whereas these foundations
are able to withstand the approximate mass
of 20 bull elephants standing on a square
centimetre of concrete – a phenomenal
feat,” demonstrated Cyril Attwell, Murray
& Roberts Construction, group concrete &
research manager.
A carbon footprint is defined as the total
amount of greenhouse gases produced to
directly and indirectly support human activ-
ities, expressed in equivalent tons of carbon
dioxide (CO
2
). “The achieved reduction in our
carbon footprint is phenomenal, especially
considering that a standard 30 MPa concrete
Foundations among the
WORLD’S GREENEST
Loeriesfontein Wind Farm has announced that its wind
turbine foundations are utilising one of the world’s lowest
quantities of Portland cement in the concrete formulation.
as supplied by the ready-mix industry equates
to a carbon footprint of approximately
300 kgs to 350 kgs of CO
2
per cubic metre,”
explained Quinn.
Traditionally, 30 MPa concrete requires
between 300kg and 350kg of ordinary cement
per cubic metre. But now scientists working
for Murray & Roberts have developed a tech-
nology that meets the 30 MPa standard using
just 25 kg of cement or even less. Not only
does it meet the standard, it far exceeds it.
To date strengths of up to 52 MPa have been
achieved on other sites using Murray
& Roberts’ patented ARC (Advanced Recrys-
tallisation) technology and 0 kg of Portland
cement per cubic metre.
The site
Loeriesfontein Wind Farm is situated within
the Hantam Municipality and will comprise
61 wind turbines each with an output of
140 MW and will generate approximately
563 500 MWh/year of clean, renewable energy
to the national grid. The wind farm will avoid
approximately 550 000 tonnes of carbon emis-
sions each year when compared to traditional
fossil fuel power plants and generate enough
to power around 120 000 average South
African households.
The site, which spans a total of 3 453
hectares, was chosen for its excellent wind
resource, favourable construction conditions
and straightforward electrical connection
into Eskom’s Helios substation. The wind
turbines will be supplied by world-leading
manufacturer Siemens Wind Power, with the
blades, hubs and nacelles that compose them
arriving from overseas at a nearby port and
being transported by road to Loeriesfontein.
The 99 m turbine towers are to be manufac-
tured by GRI, in Atlantis, in the Western Cape.
Civil and electrical works are to be completed
by a consortium comprised of Murray and
Roberts Construction and Consolidated
Power Projects.
The Loeriesfontein Wind Farm is part
of the South African Government’s Round
3 Renewable Energy Independent Power
Producer Procurement Programme
(REIPPP) is expected to be operational
by December 2017.
>
“Cement manufacturing is
typically a highly energy
intensive process. By
substituting the cement with
a by-product such as GGCS,
we are able to reduce our
carbon footprint considerably.”