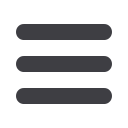

56
TUBE PRODUCTS INTERNATIONAL May 2017
www.read-tpi.comNew tube cutting technology
meets next generation
production needs
By Geoff Shannon, Amada Miyachi America, and David Van de Wall, Amada Miyachi Europe
Replacing legacy cutting systems
The pulsed neodymium-doped yttrium aluminium garnet
(Nd:YAG) lasers used in the past two decades have definitely
been great workhorses. They have performed well and been
excellent manufacturing centres for many companies.
Unfortunately, the original integrated pulsed Nd:YAG
lasers that remain in operation are now obsolete and
difficult to service.
While many of these systems have been upgraded
to fibre lasers, they still have old stage sets that are
a number of generations behind current technology.
In addition, they are running on slow and ageing
controllers with legacy software.
Simply put, the laser, stages, controller, software,
water systems and automated tube loader technology
have all moved on.
Here is a brief overview of improvements in these
components that enable faster and better cuts with
higher production rates and less down time.
S
tents and tubes are used in countless medical
devices and new ones are being added every day,
fuelled in part by the growth of minimally invasive
surgery and the commonplace use of stents. The sheer
number and diversity of devices is rapidly increasing,
and with it the demand for more and more laser cut
stents: flexible tubing, cannulas and micro cannulas,
needles, biopsy devices and other minimally invasive
tools.
Figure 1
shows examples of common features in
modern stents.
While legacy stent and tube cutting systems have
performed well during recent decades, new cutting
technologies coming onto the market offer faster and
better cuts, with higher production rates and new and
unique cutting capabilities.
Laser
The pulsed Nd:YAG lasers used in the past have been
superseded by fibre lasers with better beam quality that
does not change with pulse energy and average power.
This provides a smaller and more consistent focused spot
size, which offers tighter cutting tolerances and, with spot
sizes down to 10 microns, the ability to cut much finer detail
features. These lasers provide pulse frequencies up to and
beyond 5 kHz and pulse widths down to 20 microseconds (µs)
to enable energy input optimisation for a wide variety of tube
materials and wall thicknesses.
Higher frequencies can be implemented to maximise
acceleration and speed for a range of part thicknesses. From
an operational standpoint, the fibre lasers have a number
of advantages. They are air cooled, run off single-phase
240V electrical power, and have diodes with lifetimes that
are greater than 70,000 hours, which equates to minimal
operational costs.
Figure 2
shows an example of a tube
produced by one of the new laser tube cutters on the market
(left) and a close-up of laser tube cutting (right).
Fibre lasers use microsecond pulses and offer a cutting speed
and edge quality that is sufficient for many applications. The
femtosecond (fs) laser offers laser pulses that are under
400x10
-15
seconds (s), or about one million times shorter than
the fibre laser. The very short pulse duration, combined with
Figure 1: Modern stents