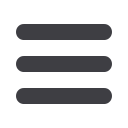

58
TUBE PRODUCTS INTERNATIONAL May 2017
www.read-tpi.comAmada Miyachi Europe
www.amadamiyachieurope.comAmada Miyachi America
www.amadamiyachi.comWater system
In many legacy system designs, the water system was a weak
point, requiring constant attention and maintenance to keep
the machine running. Such issues as small water tank sizes,
short lifetime pumps and lack of internal flow monitoring all
added up to an unreliable system. Compounding these issues
is the fact that it was difficult to access, even to simply change
water filters. Fast forward to newer systems, which have
a ten-gallon tank size, four-level debris filtering, intelligent
programmable flow valves, multiple solenoid switches to
prevent large water leaks, and drawer-mounted hardware that
enables filter changing in seconds. The user interface provides
the operator all necessary information, along with pre-cutting
safeguards and go/no go limits to ensure that all is well.
Automated tube loaders
The standard stent and tube cutter is loaded manually with
tubing that is typically up to 3m long. The cutter then cuts
parts and advances the tube according to the program. At
some point, the amount of tube remaining is of insufficient
length to make the cut, and the remainder is removed and a
new tube loaded. With more pressure to improve productivity
and minimise labour costs, many are now using automated
tube loaders to feed the cutter tubes. While this is not new,
there is now an increased potential for using these tube
loaders for automated wet connect on tube diameters larger
than 1.5mm. Although one should not operate the tube cutter
in a totally ‘lights out’ mode, using the automated loader can
significantly reduce labour allocated to the machine.
Open architecture system design
A key part of any system is making the hardware usable for the
operator on an every-day basis. One feature that contributes
to this is using composite over granite with better vibration
damping. Because the composite has a uniform internal
structure, it can be mechanically modelled and so optimised
for vibration isolation, load bearing capacity and deflection
under load. This enables a cantilever arm to support the focus
optics and z and cross axes stages, providing a very open
machine from an operator accessibility perspective.
Systemdesign and cutting performance of the latest generation
stent and tube cutting systems offer significant advantages
and capability over legacy machines for increased productivity
and enabling product innovation with better process capability.
Whether using the fibre or femtosecond laser, improvements
to motion, controller and control software make the latest
stent and tube cutting system superior to legacy systems or
provide new capability for future manufacturing needs.
Figure 3: Examples of femtosecond laser cutting of fine features
(a)
50 micron slot in 250 micron OD
Nitinol tubing
(b)
50 micron relief holes for flexible tubing
(c)
Edge quality of Nitinol stent
with only ultrasonic bath cleaning