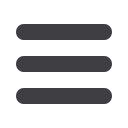

108
S
eptember
2009
www.read-tpt.com›
ORBIMATIC
Orbitalum Tools GmbH
Germany
Phone: +49 6408 9026 0
orbimatic@t-online.deORBIMATIC Ireland & UK Office
Phone: +44 1733 555 285
info@orbimatic.co.ukwww. o r b i ma t i c . c om
Next Generation
Orbital Welding
Equipment
ORBIMAT 165 C
A
dvanced
- Single dial operation
- Graphical operator guidance
- Auto programming
BUP Control
sectional control of inside purge pressure
Flow Force
reduces gas filling time of closed weld heads
down to 10 sec
Compatible with all
ORBIMATIC weld heads:
Enclosed
weld heads
Open arc
weld heads
Tube to tubesheet
weld heads
Visit us in
Hall I
Booth 229
A
dvances
in
C
utting
, S
awing
& S
awblades
THE new TruLaser Tube 7000 laser cutting
system from Trumpf Inc, USA, processes
tubes inside a tunnel-like safety enclosure
and then, depending on size, moves them
forward to the brush table or ejects them
to a parts container behind the machine. It
features heavy-duty drives engineered for
heavy tubes, a broad chucking range and a
high degree of flexibility.
This machine can cut tubes and profiles
with large diameters and wall thicknesses
without sacrificing productivity and it is
able to process tubes up to 30ft long and
can handle a maximum weight of 496lb.
The system has a 0.6 to 10" clamping
range, and is available with up to 3.6
kilowatts of laser power, making it suitable
for a wide range of applications.
Trumpf states that the TruLaser Tube 7000
can boost productivity, compared with
conventional processes like sawing, drilling
or milling. It claims one example of a
productivity enhancement is the short set-
up time when changing programs. Nearly
all of the adjustments depend on profile
specifics and values that have to be entered
at the machine and the loading unit can
easily be handled by the parts program.
The self-centring chucking jaws do not need
to be changed and the rollers that provide
support and lateral guidance for the tubing
automatically adjust to the diameter. Even the
integrated scrap container in the feed station
is emptied without operator intervention.
The FocusLine function automatically
adapts the laser focal position to the
material type and thickness. The machine’s
software independently adjusts to the focus
parameters given in the technology table,
eliminating any set-up problems. A new
slender cutting head with a 6" lens and
new clutch is designed for flexibility and
process safety, the company claims.
When combined with the LoadMaster Tube,
featuring a tube magazine holding 8,000lb of
raw material, the TruLaser Tube 7000 can
be also be fully automated. Its pivoting feed
support holds a number of tubes and keeps
them at constant orientation. The loading
unit performs a feasibility test to compare the
tube geometry with the parts program and
special profiles and small batches can be fed
by a conveyor section. The LoadMaster Tube
measures the pipe length and adjusts the
position of the grippers accordingly.
The TruLaser Tube 7000 works with a
new version of TruTops tube software to
make sophisticated processing strategies
available and this software is built around
a database that contains all of Trumpf’s
technical knowledge.
With this newsoftware, complex tubedesigns
can be fabricated more easily, precisely and
reliably. It is now possible, for example, to
position one 3D tube on another instead
of designing and programming individual
tubes. This saves time since parameters
such as length, width, height, wall thickness
and spacing between cut-outs can readily
be modified to generate any number
of variations.
Trumpf Inc
– USA
Fax
: +1 860 255 6424
Website
:
www.us.trumpf.comTruLaser Tube 7000 tube cutting system
paves the way to new fields of application
Trumpf’s TruLaserTube 7000