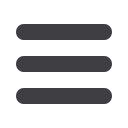

T
echnology
U
pdate
60
S
eptember
2009
www.read-tpt.com›
It says it is possible to replace single
mould blocks quickly, and a complete mould
block set consisting of 82 pairs of blocks
can be replaced by two operators within
only 30 minutes. This hopes to keep any
interruptions in the production process to
a minimum.
Unicor presented the UC 125 during an
in-house show in May, in its technical lab in
Hassfurt. Impressed by the speed, a visitor to
the symposium said that the UC 125 “might
be the fastest corrugator in the world”.
Unicor’smanagingdirector,KlausKaufmann,
said: “The UC 125 is not only fast and
efficient. The corrugator is furthermore an
important tool for pipe producers that, when
focusing on output and price per metre,
can help customers to remain one big step
ahead of the competition.”
Unicor GmbH
– Germany
:
sales@unicor.deWebsite
:
www.unicor.comUNICOR, Germany, is a manufacturer of
corrugated pipe extrusion machinery and
it claims its UC 125 corrugator has been
designed to allow producers to reduce the
cost of production while simultaneously
increasing output of plastic pipe.
It says the machine can produce double
wall pipe with the nominal size of 110mm
at 30m/min, compared to an average speed
of around 18m/min for other corrugator
machinery available on the market.
The company attributes the high production
speed to a new developments in the
cooling system and the mould blocks.
Unicor’smanagingdirector KlausKaufmann
commented: “Our new technology
enables pipe manufacturers to replace
two corrugators that worked with average
speeds by the faster UC 125.”
According to Unicor, one main focus of
the development department has been the
reduction of operation and maintenance
costs. The result is that the number of
wearing parts could be minimised, and the
change of wearing parts can be executed
much faster. The Unicor staff optimised the
curve geometry of the mould block in-let and
out-let in reaction to the higher mechanical
requirements and the demoulding of the
forming blocks has been extended by
an additional demoulding element. These
developments ensure an extension of the
components’ lifecycles.
Corrugated pipe production at 30m/min
Visitors at the UC 125 symposium watching the
corrugator’s starting process
The outlet of the UC 125 during pipe production
Cutting out
deviations in
repeatability
measurements
A NEW ‘robotically’ programmed measuring
technique that aims to radically improve
repeatability measuring consistency has
been developed by TeZet Technik AG,
Switzerland. The tube-specialised software,
TeZetCAD, is modularly structured and has
more than 100 tube functions. It is also
menu driven, making it more user friendly
and accurate than previous technology
available to the industry.
The measurement process has always
been time consuming and complex for
tube measurements. For example, optical
measurements using fixed cameras to
measure a fixed tube are only accurate
when the tube has no re-entrant angles or
add ons. The process is particularly fraught
with difficulty when it comes to bending
tubes, with many attempts often needed
to get it right, often wasting material and
time. TeZetCAD claims to ensure that the
bent tube is correct almost immediately due
to the software’s built in bender correction
processes.
TeZet adds that other techniques can result
in bent tubes springing back and claims
that using its measuring software removes
this possibility of error, however complex
the pipe is.
TeZet Technik AG
– Switzerland
:
tezet_leistritz@compuserve.comWebsite
:
www.tezet.com