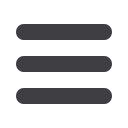

T
echnology
U
pdate
68
S
eptember
2009
www.read-tpt.com›
WARRIOR, UK, claims to have come up
with a solution to the problem of accurately
controlling the direction of moleing
systems.
Accuracy is key when installing new pipe
with mistakes potentially causing disruption
to the surface, or damage to other services,
negating the environmental benefits of using
trenchless technology in the first place, and
the company says that, with directional thrust
boring, these issues can be minimised.
Full-directional control Warrior equipment
uses detection technology located in the
head of the rod to accurately establish its
location underground to within millimetres
at any one time. The rod can be directed
around obstacles such as tree roots, other
pipes, ducting and services until it emerges
into the receiving pit.
“Both the WR4 and WR6 work from
compact starting pits and thrust a series of
connecting rods into the ground,” explains
Tony O’Brien, Warrior’s managing director.
“Once the rods are in
place the pipe or cable
to be installed is attached
to an expanding head in
a receiving pit. The pipe
or cable is then pulled
into position and the rods
are removed from the
launch pit.”
The WR4 only needs
a launch pit measuring
approximately 10cm wide
by 15cm to operate and
Taking control of trenchless technology
is easily manoeuvred into place within
the pit due to its compact and modular
design. Lateral connections can be easily
undertaken from open trenches.
“The WR4 boasts a pushing rate of up
to 2.7 metres per minute yet only weighs
168kg, so it can easily be manoeuvred
and operated by just two people,” said Mr
O’Brien. “The WR4 is capable of installing
a 100mm diameter pipe and the WR6 up to
225mm, both in very compressed soils.”
Warrior
– UK
Website
:
www.warriorworldwide.comSHEAR-FORMMachine Tools Ltd, is a sheet
metal and plate working machinery supplier
and sole UK representative for Swiss
coil processing equipment manufacturer
Soprem Automation AG.
The automatic and manual strip welding
machines available from the company
provide an economical solution for joining
the strip end from a processed coil with the
beginning of a new coil.
Soprem variable speed SGA strip-end
TIG welding machines, with automatic
strip cutting, strip positioning and welding,
provide component fabricators using coil
strips in their production with the capability
to weld 0.2-1.5mm thick coils strip in
widths up to 250mm using both DC and
pulsed welding.
Automatic and manual
strip welding solutions
An automatic strip end welder
This equipment is able to store up to
100 different welding parameters, including
start, main and end-current flows.
The integrated management control system
provides the user with fast repetitive welding
of different types of coil strip.
The variable speed BSM three-phase, 230V,
manual strip-end TIG welding machine has
the capability to join 0.2-1.5mm coil strip
in widths up to 250mm using both DC and
pulse welding.
Up to 100 different welding parameters
can be stored, including several start and
stop ramps. This machine, which is highly
mobile, is supplied with gas flow meter,
cutting unit with cut-out die and an electrode
grinder.
Shear-Form Machine Tools Ltd
– UK
Fax
: +44 2476 695601
:
sales@shear-form.co.ukWebsite
:
www.shear-form.co.uk
The WR4 (below and left) and WR6
(bottom left) in action