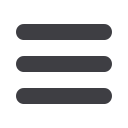

4
Mechanical Technology — October 2016
⎪
On the cover
⎪
P
eter Austin has been involved
in the manufacturing of pneu-
matic components for his entire
professional life. To date, he
has accumulated 28 years of service at
SMC, 20 of which were as manufacturing
manager at the UK facility, which recently
celebrated winning the Award for Manu-
facturing at the local (Milton Keynes)
Business Achievement Awards, 2016.
“The UK facility is a made-to-order
SMC subsidiary that manufactures
mostly special products – over 90%.
They make standard products for urgent
out of stock orders, for example, but
prefer to focus on products that need
to be customised or those that are not
immediately available off the shelf. This
policy is driven by the company’s guiding
philosophy of customer-centric design
and ultimately, customer satisfaction,”
says Austin.
With a significantly bigger market,
SMC began in the UK 38 years ago.
Today, the facility has 230 internal staff
with a nationwide sales team of around
120 technically trained sales engineers.
“There is a strong electronics and
semi-conductor industry in the UK, so
the trend is to focus on smaller products
for lighter applications. Here in South
Africa, heavy industries such as mining
are stronger, so there is a shift towards
the larger ranges,” he points out. As well
as its widespread use in automatic manu-
facturing systems such as those used
by the automotive industry, pneumatics
is widely used in an array of industries
including food and packaging, machine
tools and many others.
In addition, “both globally and in
South Africa, we are the number one
supplier to the Japanese automotive
industry and are equipped to deal with
all automotive companies,” he says.
“Generally speaking, we pride ourselves
on strong relationships with the Japanese
automotive industry.”
SMC South Africa’s production
capabilities
SMC’s newest manufacturing facility, is
modelled to achieve Japanese quality
levels and to mimic long established
manufacturing principles. Although
smaller compared to the larger mass
production sites in SMC’s portfolio, the
company’s production structure ensures
lean and efficient manufacturing. “All of
our factories operate according to SMC’s
production guidelines, from raw material
storage to machining of components and
then on to the assembly and testing of
completed units,” says Austin.
The actuator production process starts
with the cutting of raw materials supplied
by SMC’s mass production sites around
the world.
These materials come into the fac-
tory and go directly into bulk storage.
Stroke related parts are cut using cut-
ting machines on receipt of a customer
order and thereafter the machining is
completed with either CNC machinery
or special purpose equipment. “Here in
South Africa, we can machine material
with diameters from 3.0 mm to 320 mm.
Both the cut-to-length and the finish-
ing machines used are designed for preci-
sion and repeatability. The operator puts
the component in, clamps it down and
performs the operation under automatic
control. Rapid changeover is then made
possible via pre-programming, even if the
following component is a different size.
“We often need to make many different,
SMC Pneumatics South Africa has invested
heavily into the local economy and into
its local production facilities, with some
machinery being the first of its kind on
African soil.
MechTech
visits the newly
opened premises and talks to head of
manufacturing, Peter Austin (right), who
brings 28 years of SMC experience from
the company’s UK facility in Milton Keynes.
Customer-centric manufacturing:
The SMC way
smaller batches in quick
succession and quick
changeover principles
ensure increased pro-
ductivity and efficien-
cies,” he explains.
Thread rollers are
commonly used to gen-
erate the tie rod and
piston rod threads for the
majority of cylinder sizes.
Following cutting and de-
burring of piston rods there are
three CNC turning machines in the fa-
cility. “These have highly sophisticated
control systems, to such and extent that
they are disabled if their position is dis-
turbed. They have built-in GPS sensors
that record the position on installation
and if any change in that position is de-
tected, the manufacturer is informed and
the machine is automatically disabled,”
Austin tells
MechTech
.
The CNC machines are mostly used
for manufacturing piston rods in the dif-
ferent sizes required. For the smallest
pistons, those with 3,0 mm to 12 mm
rods, a Tsugami precision CNC machine
is used: “These are watch-making
machines for very small but accurate
components.
“Here in South Africa, the smallest
size we do is the 3.0 mm rod for our
6.0 mm CJ2 cylinders,” he says, add-
ing, “all the CNCs will also cut threads,
but for the very small sizes, a three roll
Fette thread roller systems is preferred.
This is an instant process and, because
the threads are formed and not cut, its
clean and debris free.”
For the larger piston rods, two preci-