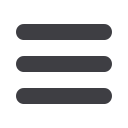

Mechanical Technology — October 2016
5
⎪
On the cover
⎪
Left above:
Materials come into the factory and go directly into bulk storage.
Stroke related parts are cut using cutting machines on receipt of a customer
order.
Left:
Thread rollers are used to generate the tie rod and piston rod threads.
Above right:
For the larger piston rods, two precision DMG Mori CNC
machines are used.
Right
: Assembly starts by attaching pistons to piston rods.
For the majority of sizes, SMC uses the roll crimping
method.
sion DMG Mori (Morisiki)
CNC machines are used,
the largest being sized for
manufacturing rods for the 300
bore cylinder from 70 mm rod, while
the middle DMG machine is dedicated
to the 16 to 30 mm rod range for the 32
to 125 mm actuators.
“These are the first machines in the
country with this level of CNC control.
DMG Mori is, itself, an SMC customer
and we provide the pneumatics for its
machines. We also supply most of the
pneumatics for other Japanese machine
tool builders.
“We use the same processes, jigs and
machines as those in our big standard-
product factories to manufacture custom-
ised products. The net result is product
with exactly the same machined quality,
without sacrificing competitiveness,”
says Austin. “All of our processes are
audited for quality in Japan and we are
required us to send samples for cutting
and testing.”
Following machining, the assembly
process begins. Pistons, rod covers,
head covers, cushion rings and other
standard internal components are stored
on the production line. Assembly starts
by attaching pistons to piston rods.
“SMC has several methods of locking
the piston onto a
machined rod.
For the smallest
sizes, we run a
thread through
the piston and
screw it onto the
end of the rod. But for
the majority of sizes, we
use the roll crimping meth-
od,” Austin notes. “The aluminium
piston is assembled onto the rod and
placed into an assembly jig to complete
the crimping,” Austin informs
MechTech
.
There are three actuator assembly
lines based on fundamentally different
methods of assembly. “We also have a
fourth assembly line for the assembly of
valve manifolds and FRLs (filter, regula-
tor, lubricators) – this is a custom assem-
bly service from standard components.
The fifth line is used to add accessories
to existing products,” he says.
“We are able to assemble everything
from the most basic to the high-tech
Industry 4.0 ready components – and
SMC can offer systems to almost any
protocol to suit its markets in every part
of the world.
“As a global company, we strive to
produce as much as possible in-house, so
we do our own die-casting, moulding and
extruding – and we even make or own
circuit boards. While some of our large
factories are 100 times bigger than this
one in South Africa, we retain the same
flow, the same degree of control and we
achieve the same product quality.
“Philosophically, SMC is driven by
customer demand. That is why this
factory is needed in South Africa, so we
can offer the same level of customised
service available to any SMC customer
anywhere in the world, along with the
same Japanese approved quality level,”
Austin concludes.
q