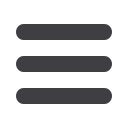

Technology News
www.read-tpt.com30
M
ay
2015
CNC metal pipe machining
COPIER Pipe Machinery (formerly
known as Copier Bevelmachines)
engineers, purchases and constructs
machinery for metal pipe finishing,
including pipe bevelling, cutting, sawing,
bending and grooving.
The latest technology is CNC-
controlled pipe bevel machinery, where
pipes are machined by mechanically
cutting away material. The machine
has radial and axial feeding. With this
feeding system all common angles can
be made without adjusting the tooling
set by hand. Another advantage is that
the wall thickness that can be handled
is unlimited.
All common bevels can be pre-set in
the machine and can be easily repeated
by the operator, who only has to enter
some parameters of the steel pipe
before starting bevelling or machining.
The machine can perform internal,
external bevel, facing, J-bevels and
many more angles.
Recent projects include a stationary
pipe bevel machine for bevelling of
metal pipe elbows, and a 24" CNC-
controlled machine for straight
pipes.
The machines are often used in
combination with one of the company’s
pipe roller benches, which support the
pipe in front of the bevel machine.
They are electrically height adjustable,
in order to align the pipe with the
clamping system.
As well as stand-alone bevel
machines, Copier offers fully automatic
production lines for pipe machining
of metal pipe bundles (mostly in pipe
mills). This means that both ends of
the pipe are automatically machined by
CNC-controlled bevel machines.
Copier Pipe Machinery
– Netherlands
Fax: +31 183 44 8028
Email:
info@copierbv.comWebsite:
www.copierbv.comThermatool welding systems
TOSÇELIK Profile and Sheet Ind Co,
a producer of precision steel pipe in
Turkey, has initiated start-up of its
new tube and pipe production mills
in Dilovasi, using induction welding
systems manufactured, delivered and
installed by Thermatool.
Thermatool currently has 275 solid-
state welders in Turkey, and Tosçelik
now has a total of nearly forty pieces of
Thermatool equipment in operation.
Thermatool’s range of CFI and
CFD induction welders were selected
and installed at the Osmaniye plant
with benefits applied from the HCT
(Haz Control™ Technology) welder.
The units supplied to Tosçelik utilise
variable frequency and dual (induction
and contact) functionality built into a
number of systems.
Jon West, Thermatool sales manager,
commented, “Variable frequency gives
Tosçelik the ability to produce tube and
pipe from several different materials,
all on the same mill, wherever possible
using existing weld rolls and the same
basic mill set-up. We also recommended
and specified two CFD dual induction/
contact welders, which provide two
welding processes in one system with
quick change capability.” Suhat Korkmaz
of Tosçelik added, “In order to ensure
our production quality we always prefer
to use high technology equipment in our
plants. We [have been] using various
types of Thermatool heating and welding
equipment in our existing tube mills for
many years successfully.”
Tosçelik manufactures a wide range
of precision pipe specifications such
as API 5CT-5L pipes, galvanised or
black water and gas pipes, natural gas
pipes, heavy series mechanical tubes,
industrial pipe, scaffolding pipe and
normalised, polyethylene, polyurethane,
epoxy, primer coated or galvanised
square, rectangular, shaped and circular
hollow sections.
Inductotherm Heating & Welding Ltd
– UK
Fax: +44 1256 467224
Email:
info@inductothermhw.co.ukWebsite:
www.inductothermhw.comTosçelik Profile and Sheet Ind Co
–
Turkey
Fax: +90 328 826 80 09
Email:
info@tosyaliholding.com.trWebsite:
www.toscelik.com.trCoolant for pipe threading
FOR some pipe manufacturers, annual
threading tool costs can be ten times
more than the annual costs of the
coolant. Quaker Chemical Corporation
has addressed this issue with
Quakercool
®
750 TP.
Optimal for the threading process, this
metalworking coolant fluid is a mineral
oil-free
micro-emulsion.
Benefits
include lubrication, short-term corrosion
protection, clean rinsing, and a wide
water-quality tolerance. The coolant
effectively
resists
microbiological
growth and does not contain chlorinated
compounds, formaldehyde release
agents, boron, monoethanolamine or
secondary amines.
A major OCTG pipe producer wished
to lower its operating costs while at
the same time improving its threading
quality and cutting insert wear.
Quaker worked closely with the
customer to gain efficiencies on the
tooling costs, which are often the
most expensive part of the threading
operation. After incorporating the
Quakercool 750 TP metalworking
coolant fluid into the threading process,
the results were up to 30 per cent
increased tool insert life used for the
pipe threading operations; decreased
downtime due to longer tool use; and a
reduction in cost per joint.
Quaker offers metalworking process
fluids and coatings for each stage of the
tube and pipe manufacturing process,
designing fluid solutions to work with
‘front-to-back’ compatibility in mind.
Quaker Chemical Corp
– USA
Email:
info@quakerchem.comWebsite:
www.quakerchem.com