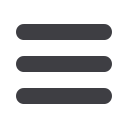

33
CONSTRUCTION WORLD
NOVEMBER
2016
Mining and industrial category winner
Husab Uranium stockpile cover & ancillary structures
The Husab Uranium Stockpile Cover & Ancillary Structures entailed the
detailing, fabrication, corrosive protection, delivery and installation of two
thousand six hundred tons of steelwork, as well as twenty-one thousand
square metres of IBR sheeting. The project duration including on and offsite
activities was fourteen months with the site duration being eleven months.
There were a number of interesting challenges to overcome, i.e. short
lead times, high specifications required by client, galvanizing of trusses,
for the logistical challenges due to cross border distances, lifting and
jacking in the 140 ton gantries and sheeting the building on forty-five
degree slopes. We pioneered some ideas at each phase to overcome the
challenges and ultimately bring the project home safely and in time.
Some highlights were:
• The logistical concern of delivering this volume of steel and sheeting
was overcome by partnering with a local transported and dedicated
trucking supplemented our in-house fleet.
• The development of the idea and plan to strand jack the gantries
(50-meter span and 140 tons) into place forty meters above ground
level, as opposed to using the traditional method of cranes, allowing
for this part of the project work to be done faster and safer, ultimately
saving the project time and the client monies.
• The development of sheeting gondola platforms, which supported a
four-man team, tools and materials. These working platforms allowed
for the sheeting installation crews to achieve around one thousand
two square metres of sheeting installation per day. The safety risk of
working on the steep slope was totally eliminated and went a long way
in ensuring that Union Steel achieved another incident free project.
• Preassembly of truss box section allowed for the site crews to lift into
place bigger sections of steelwork, minimising works being carried out
in the air, again target our approach to ensuring that our focus on all
projects is safety first, and driven with this mind-set.
Tubular category winner
Siesa Ramabodu Stadium
Scooping the award for best Tubular Steel structure was Siesa Ramabodu
Stadium in Bloemfontein. Home to Bloemfontein Celtic, the Stadium
was renovated to better serve the community by increasing its capacity,
comfort and quality as a sporting venue.
When interviewed regarding this project, the first aspect architect
Aadil Bham commented on was the professional and excellent manner in
which the team collaborated while executing this project. “All contrac-
tors and subcontractors really came together well to give us a good
final product.” says Bham. The project came about from a collaboration
between the Mangaung Municipality and the Freestate Department
of Sports, Arts, Culture and Recreation, and the Department of Public
Works. They identified this site as a priority for development within the
municipality and developed a wishlist in terms of what they wanted to
achieve. Their main priority was the upliftment of the sports offering from
this facility, bringing it to a contemporary standard. They also wanted
to create a facility that provided a quality experience to the community,
with soccer being such a loved sport in the area.
The structural frame of Seisa Ramabodu Stadium consists of main
raker beams, frames or columns which are founded on solid rock, with
seating panels and a box gutter frame bolted to a structure cast into the
concrete, carrying a cantilevered roof. The cantilevered roof spans about
30 m and consists of triangular trusses, constructed from circular hollow
sections. The trusses vary from 2 m at the back to 500 mm at the nose
cone, with a curved bottom member. It has IPE profile purlins that span
9 m (more or less the span of the raker beams) with curved cladding rails
fixed to the back of the concrete frames, which carry the circular purlins
that support the curved cladding.
The main challenge was casting in the structure that carries the
gutter boxes at the back. This resulted in variable items, and the need to
align trusses in order to create an even visual line, which contributes to
the aesthetic of the stadium. Between the engineer, contractor and archi-
tect a three member connection was designed to solve this challenge. All
aspects were surveyed, and each section had its own cleat made to align
the trusses and achieve an even visual alignment.
ON