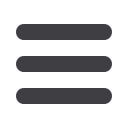

EuroWire – May 2009
55
technical article
Another advantage of the ROV was its
ability to provide real-time high-resolution
video images via a high-resolution camera
and sophisticated lighting, as seen in
Figure 3
.
Since the ROV’s buoyancy, yaw and
pitch could be adjusted on the fly, this
ROV could be very effective on missions
requiring tricky manoeuvres.
3.4 Disadvantages
The Deep-Sea ROV was designed for a
niche application. Because it was a slow
moving vehicle (< 3 knots) and it had a
finite amount of battery life, the ROV had
to be placed in very close proximity to the
inspection site.
A majority of the time it would be carried
to the site via a manned submersible in a
launch and recovery enclosure (LARE) as
seen in
Figure 4
. The BOT could operate in
currents of 2 knots or less.
4 Hybrid AUV/ROV
4.1 Purpose
The purpose of the hybrid vehicle is to
take the advantage of the Deep-Sea
ROV technology and couple that with
the advantages of an autonomous, free
swimming vehicle. This was achieved by
using a Myring hull design vice the box
shape of the first generation Deep-Sea ROV.
The Hybrid AUV/ROV is capable of greater
distances as well as the handling of strong
water currents. The Hybrid AUV/ROV has
two modes of operation: (1) autonomous
and (2) ROV. In the autonomous mode, the
vehicle can be programmed via mission
planning software to operate using
waypoint navigation. In this mode the fibre
optic tether can be used to monitor the
vehicle’s activities and allow the operator
to take control of the vehicle at any time.
Additionally, if the fibre optic tether were
to break, the vehicle is pre-programmed
to return to a selected location for
recovery. In the ROV mode, the operator
can take control of the vehicle to conduct
inspections such as to check damage on
hulls of ships, potential faults in dams, and
leaks in potable water tunnels.
4.2 Description
The shape of the Hybrid AUV/ROV is
drastically different from that of the
original Deep-Sea ROV. The profile of the
vehicle mimics the contours of a standard
submarine or torpedo design.
The body shape allows the vehicle to
speed (> 3.5 knots) through rough waters
and heavy currents.
The Hybrid AUV/ROV is 6" in diameter and
over 62" in length. Though larger than the
Deep-Sea ROV, it has the agility needed
to position itself for near field inspections.
The vehicle has a main propulsion screw
for forward and reverse motion as well as
vertical and lateral thrusters located in the
fore body. Refer to
Figure 5
for a schematic
of the AUV/ROV.
The Hybrid AUV/ROV is similar to the
Deep-Sea ROV in that it has an onboard
power supply and is tethered to the
command station via the same Deep-Sea
ROV cable. Cable is paid out of the
vehicle in a more simplistic manner than
the original Deep-Sea ROV, storing up
to 2,000metres of cable within its hull.
The tether leaves the vehicle via a small
tube called the stinger, so as to prevent
the cable from getting caught up in the
propulsion system.
The Hybrid AUV/ROV has improved
electronics and sensors to allow it to
perform its role as a piece of inspection
equipment.
4.3 Advantages
The Hybrid AUV/ROV has the capability
of travelling long distances without any
human intervention via its autonomous
operation mode.
The advantages of the autonomous
mode are that: (1) it provides a stand-off
capability from the work site and (2) it
eases operator loading by not having to
steer the vehicle at high speed over a long
distance. Without a stand-off capability,
the Hybrid AUV/ROV would have to be
delivered to the work site via a manned
submersible, more like the Deep-Sea ROV.
Additionally, the vehicle’s autonomous
capability provides a means to recover
the vehicle if the fibre optic tether were
to sever or break during the operation.
The vehicle can be pre-programmed
prior to the start of the operation
with a geodetic location to return to if
communication is lost. This could be as
simple as a single location or instruction
to swim out on the same path as was used
to reach the work site.
To assist with autonomous navigation the
Hybrid AUV/ROV is equipped with a GPS
(Global Positioning System). The vehicle
can be programmed to come to the
surface during transit to the work site to
obtain a navigational fix. Once the fix has
been obtained the vehicle can correct its
course and proceed to the next waypoint.
The vehicle is also equipped with
high-frequency sonar, as seen in
Figure 6
,
which is employed for obstacle avoidance
and to help locate the work site.
Once the Hybrid AUV/ROV has reached its
destination the operator shifts to the ROV
mode and monitors the high-resolution
imagery available from the two video
cameras. One camera is located on the
nose and the other on the GPS mast.
The camera located on the GPS mast
is used both surfaced and submerged.
This camera can assist with navigation
when surfaced and provide a different
perspective when submerged since
the nose of the vehicle is visible in the
viewing area.
In addition, the Hybrid AUV/ROV has two
lasers located on the nose, used to provide
a fixed reference frame for sizing objects
seen through the nose camera.
4.4 Disadvantages
The Hybrid AUV/ROV was not designed to
penetrate shipwrecks or small void areas;
the long length of the vehicle offsets the
small diameter size.
Figure 3
▲
▲
Figure 4
▲
▲
Figure 5
▲
▲
Figure 6
▲
▲