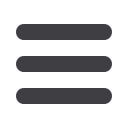

EuroWire – May 2009
56
technical article
While highly manoeuvrable, this vehicle
is better suited for external vice internal
inspections. With today’s technology, this
was the most compact unit that could
be built and still retain the sophisticated
features described above.
5 Review of test results
5.1 CommScope Testing
Standard outside plant cable testing was
completed at the CommScope facility
located in Claremont, NC. This testing was
performed, not to qualify this cable for
use as an everyday terrestrial cable or long
haul oceanic cable, but in order to set a
benchmark for future deep-sea fibre optic
cable designs. The cable was subject to the
most severe requirements set out in the
ANSI/ICEA S-87-640-2006, the GR-20-CORE
and the EN 187105 standards, and tested
to failure under the general guidelines of
these specifications.
5.1.1 Compression to failure
The Telcordia GR-20 was the most
stringent of the three standards, calling
for 44N/mm of pressure over a one minute
period and 22N/mm of pressure over
ten minutes. A similar test was adopted
by applying a specified load for a period
of ten minutes, and then testing the
attenuation of the cable at the end of
that time period while the cable was still
under load.
The GR-20 standard had the most
rigorous requirements for any increase in
attenuation; therefore the GR-20 was the
guideline that was followed. The standard
stated that the change in attenuation
should remain less than 0.05dB for 90% of
the fibres under test and less than 0.15 for
100% of the fibres under test.
The cable was crushed using a 25mm steel
plate with rounded edges having a 10mm
radius. A schematic of the test setup can
be seen in
Figure 7
.
With every passing result, the load was
increased. This procedure was followed
until a cable failure was achieved.
The results of this testing can be seen in
Table 2
.
As we can see from the results,
the cable performed surprisingly well,
considering that the requirement for a
standard outside plant cable is 44N/mm.
Each of the pressures was performed
twice in order to assure a passing or a
failing result. The incompressible fluid
within the cable may have attributed to
the performance of this cable construction
under a compressible load.
5.1.2 Impact to failure
The EN-187105 standard required a
specified impact force be applied once
over three different sections of the cable.
The ICEA-640 standard required a specified
impact force be applied twice over three
different sections of the cable.
The GR-20 standard required a specified
impact force be applied 20 times in one
location on the cable. In a real underwater
scenario an impact would most likely
occur only one time in one location,
therefore the GR-20 test procedure was
followed. The GR-20 standard had the
most severe requirements for any increase
in attenuation; therefore the GR-20 was the
guideline that was followed.
Again, the standard stated that the change
in attenuation should remain less than
0.05 dB for 90% of the fibres under test and
less than 0.15 for 100% of the fibres under
test. A schematic of the test setup can be
seen in
Figure 8
.
The test cable was impacted with a
specified force for the duration of one
cycle. Once the impact was complete,
the cable’s attenuation was tested.
This procedure was repeated until a cable
failure was achieved. The results of this
testing can be seen in
Table 3
.
From these results it can seen that 0.4Nm
is the maximum impact force that this
cable could withstand. At 0.5Nm the
cable was completely flattened with the
broken fibre protruding from the side of
the jacket. As a reference, standard outside
plant is required to withstand an impact
force of 4.4Nm, much higher than what
the Deep-Sea ROV cable was capable of
achieving. However, this cable will most
likely be impacted under water; any falling
object located underwater will move with
much less velocity, hence much less force
will be exerted on the cable.
5.1.3 Tensile to failure
All three standards require a specific
tensile load with the ICEA-640 and GR-20
standards calling for the highest short-
term tensile load at 2670N. The EN-187105
calls for a short-term tensile load that is a
factor of the cable’s weight. The mandrel
diameter used on the bench was specified
to be the most stringent in the GR-20 and
ICEA-640 documents. These standards
specify a maximum diameter of 560mm
and a minimum of 30x the diameter of the
cable. Testers utilised a mandrel diameter
of 26mm for this test.
According the ICEA-640 and GR-20
documents, a cable failure constitutes
an attenuation increase of greater than
0.05dB at the 1,550nm wavelength and/
or a fibre strain greater than or equal to
60% of the fibre’s proof strain. Obviously,
this test would not be approaching the
specified loads, as the cable has a modulus
of elasticity in the range of only 12kgf.
Testers used an Instron® tensile bench with
built-in extensometer to strain test this
cable. The tensile bench was set up to run
as slowly as possible, to allow for recording
Figure 7
▲
▲
Figure 8
▲
▲
Pressure (N/mm)
Delta (dB)
Pass/Fail
10
0.00
Pass
15
0.08
Pass
20
0.03
Pass
25
0.11
Pass
30
0.70
Fail
Number of Impacts
Force (N.m)
Δ Attn.
Pass/Fail
1
0.1
0
Pass
1
0.2
0
Pass
1
0.3
0
Pass
1
0.4
0
Pass
1
0.5
N/A
Fail
Table 2
▲
▲
:
Compression Test Results
Table
▲
▲
3
:
Impact Test Results