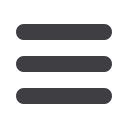

C U T T I NG , S AW I NG & PR OF I L I NG
www.read-tpt.comSEPTEMBER 2017
103
High-speed flying cold saw
powered by U-Trak technology
UNIVERSAL Controls Group (UCG),
a manufacturer of industrial control
systems, has introduced U-Saw, a
high-speed flying cold saw for tube
mills equipped with the company’s
Length Control System.
The new flying cold saw is available
in both single and double blade version,
in sizes ranging up to 16" and speeds
up to 300 fpm.
The U-Saw can use either TCT or
HSS blades. The 76mm (3") version
of the U-Saw will be featured at the
FABTECH show in Chicago, USA, in
November on Universal’s booth (Tube
& Pipe Hall, Booth B10057).
UCG builds new control systems,
die accelerators, drives and other
accessories to retrofit new or existing
machinery in almost any industrial
environment. Located under one
roof with a used machinery dealer,
Universal Tube & Rollform Equipment
Corporation, their relationship enables
them to offer a wide array of services.
Universal Controls Group
– USA
Fax:
+1 419 874 2825Email:
sales@universalcontrolsgroup.comWebsite:
www.universalcontrolsgroup.comResponsiveness builds customer trust
WINTON Machine Company produces
tube fabrication equipment and other
engineered solutions for customers
in the USA and in countries across
Europe, South America and Asia.
The company’s machines have been
utilised by companies in industries such
as HVAC/refrigeration, electronics,
aerospace and military.
Celebrating its 20
th
anniversary in 2018,
the company partly credits its success to
its responsiveness to customer requests.
“Our customers know they can share
their production improvement needs
with us and receive custom-engineered
options to existing Winton-produced
machines,” said George Winton, PE,
president, Winton Machine Company.
“When we get emails and calls asking
for design help or improved efficiencies
from customers or prospective ones, we
are very responsive. Once the discovery
process is complete, our team works to
find the best upgrade or option. We’ve
even created an innovative new machine
design altogether. We are agile and
flexible in our engineering design work
which has allowed us to produce over
100 different tube fabricating machines.”
As an example of the requests the
company receives, an existing customer
asked, “Our tubing supplier identifies
defects in the spool by painting that
section of tubing. Do you have a way
to cut this section out and discard
automatically?”
This customer uses one of Winton’s
free-standing, all electrical tube cut-
off machines that automatically feeds
and cuts from a bulk spool of tubing
(level wound spool) or straight lengths.
The CTL-23PA automatic tube cutter
makes use of two backup rolls and one
chipless type cutter to cut through small
diameter tubing.
With the tubing clamped, the backup
rolls and cutter both move in to make
the cut. As the cutter continues to come
in, the backup rolls plateau on the tube’s
outside diameter, providing support
during the chipless cutting process.
Dubbed the ‘black mark detection’
option, the engineering team worked
to design and build an automated
solution for the CTL-23PA that would
sense defects marked on tubing and
then remove only that section of the
tube before being used in the next step
of production. The Winton engineering
team determined that an additional
option needed to be designed and built
to discard the defective section after it
was cut. An off-load table with a diverter
was the solution that allows the ‘good’
tube material to continue into production,
while the ‘defective’ section is sent in a
different direction.
Manufacturers
producing
parts,
commercial equipment or consumer
products for the refrigeration industry will
be aware of the issues related to tubing
imperfections.
Another option for the CTL-23PA
includes software features that enable
the user to manage multiple types of
cuts. Improved robust guarding was
added for operator safety. Winton’s
standard on-board diagnostics makes
the machine simple to operate, and the
tube straightener has digital pressure
control to compensate for the difference
in the tubing’s wall thickness. The CTL-
23PA automatic tube cut-off machine
comes standard with programmable
part quantity and programmable cut
length. 80 psi shop air ensures the tube
is clamped. Winton Machine will be
exhibiting at FABTECH 2017 in Chicago,
Illinois, USA, from 6 to 9 November.
Winton Machine Company
– USA
Email:
sales@wintonmachine.comWebsite:
www.wintonmachine.comU-Saw high-speed flying cold saw