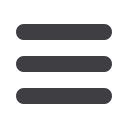

C U T T I NG , S AW I NG & PR OF I L I NG
www.read-tpt.com106
SEPTEMBER 2017
Fully automatic CNC machine
SIMEC from Italy offers a fully automatic
CNC machine designed to utilise
DMO5 circular saw blades and all their
derivatives. The machine can cut to any
pre-programmed angle of ±60° and has
the ability to cut intersecting angles on
the end of a wide selection of material
types. With a choice of three loaders
the machine is suited to load and feed
both symmetrical and asymmetrical
profiles.
The CNC control uses a sophisticated
program that is able to process all the
data and then select and optimise this
to give the greatest efficiency with the
minimum of waste. Particular attention
has been paid to reducing the scrap
end of the material so that this can be
as little as 20mm.
The material in-feeding is servo
controlled, as is the head rotation; with
this the tolerances of the cut pieces
are maintained to a high accuracy
making this suitable for robotic welding
systems. The saw can be linked to a
deburring machine or multi-discharge
feature (the standard version has
three-position discharge).
Simec
– Italy
Website:
www.simecsrl.itCutting heavy ID scarf
GEBRÜDER Lennartz GmbH & Co KG, from Remscheid, Germany, a
manufacturer and supplier of carbide-tipped circular saw blades for the ferrous
and non-ferrous industry, has launched another product in the ECOmax range.
The newly developed ECOmax – Scarf circular saw blade is customised for
cutting tubes and profiles with heavy ID scarf on flying cut-off units. Previously,
conventional blades were heavily damaged after only a few cuts because they
cut the high strength weld bead inside the bottom of the tube. The service life
of the blades was poor and the cost per cut was high, resulting in a cutting
application that was not economical.
Because of its special tooth form and cutting geometry, and in combination
with a new proprietary coating, the ECOmax – Scarf saw blade is suitable for
this application. The new design works successfully on single-head machines
as well as on twin saws with the simultaneous operation of two saw blades.
Successful trials and ongoing production usage together with target
customers and machine manufacturers have shown that the ECOmax –
Scarf blades achieve up to 7m
2
of material removal on welded tubes with wall
thickness up to 14mm. Further wear life tests and enhancements are planned
to improve the blades’ performance.
Gebr Lennartz GmbH & Co KG
– Germany
Fax:
+49 2191 9960 60Email:
info@lennartz.deWebsite:
www.lennartz.deHeinemann Saw Company
– USA
Fax:
+1 330 456 0318Website:
www.heinemannsaw.comThe Mec-120 CNC from Simec
ECOmax Scarf blade from Lennartz