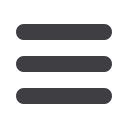

AR T I C L E
Advanced Machine & Engineering/AMSAW
www.read-tpt.comSEPTEMBER 2017
117
Key calculations for maximising tool life
in carbide saws
By Christian Mayrhofer, Manager R&D, AME, and Willy Goellner, AME
Theoretical analysis, calculation
and practical identification
Torsional vibrations are hard to measure because of the
rotating elements (gears, shafts) that are inside a closed gear
case and not easily accessible.
However, knowing the exciting torque, passing through
the gear train and the gear data, critical vibrations such as
resonance can be calculated and analysed.
The following calculations and theoretical analysis are perhaps
boring for most individuals dealing with carbide saws, but they
show that much can be theoretically analysed, where practical
limitations exist.
A well experienced carbide saw specialist will be able to
analyse torsional vibration from the noise level, the cut
surfaces, and the form of the chips. He will, however, have
difficulty pinpointing where the trouble starts and what to
change in order to solve the problems.
In every gear train torsional vibrations and torsional natural
frequencies can cause significant problems if not addressed
properly.
One approach to realise basic effects and parameters is to
discretise every shaft in stiff inertias and massless torsional
springs which connect these inertias.
This has been done for a simple one-stage gear train with four
inertias and three degrees of freedom since inertia two and
inertia three are coupled with the ratio. After having modelled
up the system in this fashion the dynamic equilibrium of the
forces can be formulated for the free body diagrams.
The result is the following set of differential equations which
has the structure:
With the concept of eigenvalues and eigenvectors the
natural frequencies and corresponding mode shapes can be
calculated.
The determinant is set equal 0 and values below are used to
calculate
λ
2
.
Example values based on a simplified portion of an AMSAW
gearbox: