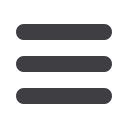

T E CHNOLOG Y
36
SEPTEMBER 2017
Expanded range of closed
chamber welding heads
THE Schweissen & Schneiden trade
fair provides members of the welding
industry with the opportunity to present
their latest innovations to the market.
The event is an excellent opportunity
for Polysoude to demonstrate its latest
developments in both the orbital welding
and automated cladding industry. These
are changes in technology that have
been driven by the desire to satisfy
specific customer requirements.
With recent global economic difficul-
ties a significant investment in
technology requires a quantifiable
improvement in productivity in return, as
well as ease of use and a boost to product
quality. Schweissen & Schneiden is an
opportunity for Polysoude to showcase
these advances.
In order to meet these demands
Polysoude has expanded its range of
closed chamber welding heads with the
new MW 34, which has an application
range of 6 to 34mm. Like the other
welding heads from this series, the MW
is easy to use, with the controls placed
directly on the handle of the head and
a high duty cycle, which meets growing
market demand.
The MW welding head not only
reduces the radial space requirements
of the micro-fittings industry, but
also the quality requirements of the
pharmacology and food industries.
Another advantage of the welding head
is the casing (TCI), used for all closed
chamber welding heads by Polysoude.
It is made of titanium and this allows a
response to variations in temperature
on the outer diameter of tubes. By using
titanium Polysoude is in a position to
provide a lifetime casing warranty and
can also help to avoid performance loss
over time in comparison with aluminium
casing.
Polysoude has also revealed the TS
8/75-2 – the latest in a series of tube-plate
welding heads. Several welding heads
can be used simultaneously thanks to
the compact and ergonomic design
of the double handle with integrated
welding and clamping controls. This
welding head has an enhanced level of
automation with its integrated AVC. With
this new series even tubes with a lower
value can be welded in assembly with the
new clamping/centring system.
The close collaboration between
users in the field and the research and
development department has resulted
in the creation of the DAQbox: a new
concept combining data acquisition
with functions enabling the optimisation
of productivity while ensuring a
reproducible quality weld.
The core function of the DAQbox
is data acquisition – an essential tool
for production monitoring as part of
the quality process. Polysoude has
added features that provide the welder
and also the quality department with
enhanced monitoring of the welding
process.
The welder can now simultaneously
monitor the smooth functioning of
the welding process and respect
the operating procedure, while also
closely following the deposit rate and
monitoring the levels of welding energy
that are being used. In a single click the
operator can choose the type of setting
to be displayed and at all times return to
the original settings.
The installation is performed very
simply with the use of a USB2 stick
with a free software licence. There is
no need for an Ethernet network. This
way the data saved during the complete
welding cycle can be read on any PC in
order to validate production.
In comparison with data acquisition
systems currently available on the
market, which consist of only six
measurements
(current,
voltage,
rotation speed, wire speed, hot wire
current and gas flow), the DAQbox
proposes the following additional data
acquisition: temperature measurement,
welding energy, wire deposition rate
and linear and analogue channels are
increased to 15 (previously five) and are
customisable by the user according to
the process requirements. Polysoude
exports more than 85 per cent of its
equipment abroad. Non-Latin languages
such as Russian and Chinese are also
available.
A major concern for manufacturers is
the length of time between the decision to
install the equipment and the moment the
equipment is ready to start production.
This is often considered to be too long.
Having engaged in years of
development and feedback Polysoude
has widened its approach to meet
shorter deadlines even for more
complex of configurations.
The new Polysoude catalogue
contains solutions to most automated
welding and cladding problems. The
company can provide the exact tool
to respond to a specific customer
problem, providing advice and enabling
the implementation of projects without
delay.
Polysoude
– France
Website:
www.polysoude.comClosed chamber welding heads