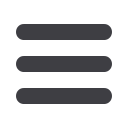

S
EPTEMBER
2016
107
BEND I NG , END FORM I NG & SWAG I NG
Flexible production cells for smar t
tube processing
PRECISELY produced tubes can help
make vital water flow or be used in
important medical devices that support
the work of doctors. Robust, short hose
connections for automotive construction
or long tubes, such as those used in air
conditioning units, also need to meet
many different requirements. Depending
on the industry and the application area,
the tubes need to be specifically formed,
bent and processed.
The networked ‘t-motion’ automation
systems by transfluid create combined
options for large series operation.
“We use our sophisticated technology
concepts for tube bending, separation,
cleaning and tube forming for the
automation systems, supplementing
them with loading systems, weld seam
control or complete handling,” said
transfluid managing director Stefanie
Flaeper.
“With the easy-to-operate production
cell coordinated in this manner,
production can start right away. The
principle clearly is one of ‘plug and
produce’.”
The specialist engineers at transfluid
integrate easy expansions such as
marking facilities, seam detection
devices, printers, tightness tests or
visual, contact-free camera systems
for inspecting geometries or surfaces,
brazing and welding units and auto-
frettage as optional components on
request. Loading systems, storage
systems, supply of the workpieces or
complete handling by robot or linear
systems can also be added.
“We coordinate the solution specifically
with the customer’s requirements,
including generation of the layout to
achieve optimised material flow and best
utilisation,” added Ms Flaeper.
Selection of handling also focuses
on the highest possible efficiency. The
devices used depend on the parts to
be produced. Ms Flaeper presented a
general principle: “Everything that can be
done to the tube in the straight condition
considerably reduces the handling effort.
From the bending machine onwards, the
robot usually takes over. Linear handling
can often be faster, more cost-efficient
and easier to reach.”
For smooth production flow, transfluid
develops its production systems to permit
loading of isometric data online from
a CAD system and to avoid elaborate
programming of robots.
The systems for loading and
separation contribute to the performance
of ‘t-motion’. Components (nuts, flanges
and screws) are supplied from splitter
magazines or rotation separators
with presence and position checks.
Additionally, supplies from the coil, or
by loading table, belt, stage, plate, chain
or vibration conveyor are available to
match the overall system.
transfluid Maschinenbau GmbH
–
Germany
Email:
sales@transfluid.deWebsite:
www.transfluid.deThe complete production cells are coordinated with
the requirements, including generation of the layout
to achieve optimum material flow
© transfluid