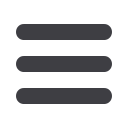

108
S
EPTEMBER
2016
BEND I NG , END FORM I NG & SWAG I NG
Automated production cell for 24/7
manufacturing
THE engineering design consultancy
Ingenium Integration has developed a
multi-function automated production
cell for H&E Knowles, a UK-based
wheelbarrow manufacturer.
The cell will speed the production
of wheelbarrow full and part frames
by eliminating many labour-intensive
aspects of production.
According to Dave Ashworth,
Ingenium Integration’s MD, “We have
developed
automated
production
cells for a number of production
processes involving tube bending. The
system under construction is the most
integrated system we have designed
to date – fully automating most of
the stages of wheelbarrow frame
production, including tube bending,
hole punching, swaging and cut-to-
length – and is designed for unattended
24/7 operation.”
Ingenium Integration bases many of
its automated production cell designs
around all-electric tube benders from
Unison, its parent company. The
system being built for H&E Knowles is
a 38mm (1.5") twin head model from
Unison’s all-electric Breeze range. It
features a left and right head on the
same carriage that facilitate precision
symmetrical bending to reduce cycle
times, with an off-set facility to enable
asymmetrical bending of the final tight
bend at the wheel end of wheelbarrow
frames, while avoiding collision with
machine architecture during the
process.
The production cell comprises a tube
bundle loader, tube orientation station
with seam detection, intermediate
dual-arm loader, bending machine and
several articulated robotic handlers, as
well as swaging, hole punching and
cut-to-length stations. It fully automates
the
entire
wheelbarrow
frame
manufacturing process, from raw tube
material handling through to final pre-
paint finishing and quality inspection.
The cell was developed at Ingenium
Integration’s
design
centre
in
Manchester, UK, and manufactured
and assembled in a facility at Unison in
Scarborough, UK. Ingenium Integration
is also able to call upon Unison’s
expertise in all-electric tube bending
technology to help solve customers’
fabrication problems. The company
holds an integration licence for the
five-axis parallel kinematic machines
(PKMs) developed by Swedish
company Exechon.
Ingenium Integration Ltd
– UK
Email:
sales@ingeniumintegration.comWebsite:
www.ingeniumintegration.com