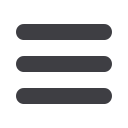

M
ay
2008
www.read-tpt.com124
›
size nearly corresponds to the grain size of the billet structure. The
grain size at the tube end is well distinguished from the grain size
in the middle of the tube. This can be explained by the two contrary
thermal processes involved: heating during the plastic deformation
and cooling down of the magnesium alloy at contact with the
extrusion tool.
An increase of extrusion ratio causes bigger grains (figure 9). During
the extrusion with an extrusion ratio above approximately 80, the
grain size decreases due to increased metal outflow velocity.
3. Drawing process
3.1 Experimental methods
Drawing was carried out at the laboratory chain drawing bench at
the Institute of Materials Science at the Leibniz University, Hanover.
The drawing bench has an engine output of 3.0kW and maximal
turning moment of 1.7kN
×
m. The maximum drawing force runs to
20kN, while velocities are 0.1-150mm/s.
Preliminary experiments have shown that thin-walled magnesium
tubes cool down very fast, so that a furnace heating before the
drawing is insufficient. Therefore a heated drawing die support was
used for tube heating during drawing. Heating is achieved by four
heating cartridges placed in a case.
For the planned experiments, two drawing alternatives were used:
sink drawing (without mandrel) and mandrel drawing
[7, 8]
. Sink
drawing is appropriate for great diameter reduction. The mandrel
drawing is necessary for wall thickness decrease.
The sink drawing of the tubes of alloy MgCa0.8 was carried out by
drawing dies with a diameter of 5.3 to 2.9mm with molybdenum
disulphide as a lubricant. The drawing velocity came to 15, 45 or
75mm/s, and the drawing tool temperature was 320 or 410°C.
After the heat exchange between tube and tool/equipment, the
temperature was measured by means of a thermographical camera.
In order to ensure a black tube surface, drawing was carried out
without deformation.
3.2 Results
If deformation grades lower than 0.1 are present during cold
deformation, it results in grain refining and a strength increase in
the first working stage (figure 10). Therefore cold drawing can be
applied as a final step in order to reach the required grain size and
mechanical properties. Analysing cold drawing made at an earlier
stage – of wire made from technical pure magnesium (99.9 per
cent) with deformation of more than 0.13-0.16 – has shown that
drawing is not practicable because of crack formation and breaking
out of tube tag.
From the technological point of view, drawing of magnesium tubes in
warm conditions is the ideal scenario. Heating of a tube was carried
out in ‘continuous furnace’ conditions, which consists of copper
tube installed on the heated drawing die case. The air temperature
variation along the furnace length can be seen in figure 11.
Table 5
:
Dependence of the tube heating temperature versus the drawing tool temperature T
D
and drawing velocity v
Т
0
(
°
С
)
320
410
v
(mm/s)
15
45
75
15
45
75
s
(mm)
0.3 0.5 0.7 0.3 0.5 0.7 0.3 0.5 0.7 0.3 0.5 0.7 0.3 0.5 0.7 0.3 0.5 0.7
Т
D
(
°
С
)
214 234 180 153 169 127 130 167 123 273 301 218 182 215 157 161 225 141
Figure 8
:
Influence of billet
temperature on grain size
Figure 9
:
Influence of
extrusion ratio on grain size
Figure 10
:
Change of structure during cold drawing