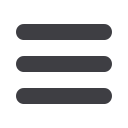

121
M
ay
2008
www.read-tpt.com›
Manufacture of small diameter magnesium tubes
with the hot extrusion and drawing processes
By Alexandr Golovko, research specialist, National Metallurgical Academy of Ukraine
Co-authors: Ch Krause, Th Hassel, Fr-W Bach
*
, Institute of Materials Science, Leibniz University Hanover, Germany
Abstract
The development of biodegradable, cardiovascular implants
(stents) made of an absorbable magnesium calcium alloy demands
an accurately defined production process. In order to evaluate the
material, magnesium alloys with a calcium content of 0.4-2 mass
per cent were used in research. The microstructure, mechanical
properties and corrosion behaviour were investigated.
Tube extrusion and the further drawing process is a very promising
concept to develop the manufacture of a semi-product for
absorbable magnesium stents. In the tests undertaken, hot extruded
tubes were reduced by a drawing process that was carried out both
with and without the use of a mandrel.
Investigation was carried out into the influence of the drawing
process sequence and certain heat treatments between the drawing
steps on the mechanical properties. Other areas were investigated
including the temperature-deformation conditions of the extrusion
and drawing processes (and their effects on tensile strength), the
elongation and the microstructure of tube samples. The results
show that an absorbable Mg alloy is available which can easily
be produced. It was found to exclusively contain essential mineral
nutrients with a non-toxic character.
1. Introduction
The demand for implants manufactured from biodegradable
materials has led to the development of production technologies
for magnesium tubes as a basic material for stents
[1, 2]
. Magnesium-
calcium alloys (MgCa-alloys) have, in contrast to other magnesium
alloys, the advantage of a very low poisonous potential during
degradation in the body.
Magnesium alloys with a content of 0.6-0.8 per cent calcium have a
particularly consistent corrosion behaviour. This behaviour could be
an indication of a moderate degradation velocity. This is necessary
in order to guarantee mechanical solidity over a certain period
and ensure a low amount of gas produced during the degradation
process.
The production of magnesium tubes can be achieved by first
producing tube pre-profiles of magnesium alloys by hot extrusion
of ingots or extruded rods. Following this, hot drawing takes place
(sink drawing without mandrel and subsequent drawing with a long
mandrel); the process ends with cold drawing that is carried out
to increase strength and improve surface quality. In order to carry
out drawing after extrusion, the tubes should preferably have a low
wall thickness at high plasticity.
The aim of this project was to determine those factors that define
the extrusion process and warm drawing of thin-walled tubes of the
alloying system Mg-Ca. It was the aim to determine the influence
of technological parameters on the mechanical properties and the
structure of the tubes.
The experiments were carried out in three steps:
1. Experiments concerning the influence of the calcium content,
deformation and temperature conditions of extrusion on the
mechanical properties of the tubes
2. Influence of the billet temperature and the extrusion ratio on
tubes’ mechanical properties and microstructure
3. Experiments of sink drawing and drawing on a long mandrel
A detailed analysis of the extrusion of magnesium alloys was carried
out in
[3, 4]
. It can be seen that details about ideal temperature-velocity-
parameters during the extrusion of magnesium alloys on standardised
industrial alloys are limited. Information about the extrusion of MgCa-
alloys or uniform results about acceptable outflow velocities and
ideal relation of container temperature to billet temperature are not
available. It is known from literature that the use of extruded billet
enables high extruding velocities
[5]
.
The authors are not aware of any other thesis that deals with the
drawing of magnesium tubes, especially of tubes made from
MgCa-alloys. In the literature that does exist, extensive facts about
the drawing of tubes of steel and nonferrous metal cannot be
transferred to the present projects with MgCa-alloys. Investigation
priorities of tubes of steel and nonferrous metal – such as energy
consumption and productivity – are irrelevant for the production of
magnesium tubes for biomedical applications. It is more important
to develop a stable drawing process and to establish the influence
of temperature and deformation parameters on the tube geometry
and properties.
2. Extrusion process
2.1 Experimental methods
Experiments were carried out with a vertical hydraulic
press with the nominal force of 800kN at the Institute
of Materials Science of the Leibniz University,
Hanover. The extrusion tool consists of a stem and
dummy block in which a long mandrel is installed,
together with a conical die (figure 1). The diameter of
the container bore is 29mm, while the ram speed is
constant and equal to 1.25mm/s.
Figure 1
:
Extrusion tool – 1) extrusion die, 2) container bore,
3) billet, 4) mandrel, 5) die