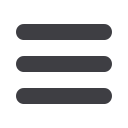

123
M
ay
2008
www.read-tpt.com›
The increase of the container
temperature in contrast to the
billet temperature (figure 4)
causes an increase of the metal
temperature in the container
and therefore a deterioration of
the mechanical properties.
For the application as implant
material alloys with calcium
content of 0.6-0.8 per cent can
be recommended
[6]
.
Therefore the alloy MgCa0.8
was
investigated
more
intensively concerning the
influence of the billet temp-
erature and ram speed on the
mechanical properties and the
microstructure.
In these experiments wall
thickness was changed to
influence the extrusion ratio
and metal outflow velocity at
the constant tube diameter
(table 2).
In figure 5 characteristic stress-
strain-diagrams for tubes of
alloy MgCa0.8 are shown. The
ratio of yield stress to tensile
strength is dependent on the
extrusion conditions of 30-60
per cent, and in parts greater.
Greater ratios can be seen
at samples with a lower yield
stress. With an increase of
billet temperature, the tensile
strength and yield stress
drop (figure 6). Elongation
firstly increases and then
remains nearly constant. The
mechanical properties correspond to the measured extrusion force
and grain sizes.
An increase of extrusion ratio leads to reduction of elongation,
tensile strength and yield stress (figure 7). The grate values of
tensile strength at the high extrusion ratios can be explained by the
fact that the extrusion process runs at a maximum extrusion force
but with much reduced ram speed.
Alloy
Extrusion ratio
T
B
= 350
°
C
T
B
= 410
°
C
R
m
[MPa]
A
5
[%]
R
m
[MPa]
A
5
[%]
MgCa0,4
55-57
–
–
177
15,7
70-74
177
18,5
179
14,4
120-130
160
12,1
199
10,3
MgCa1,2
55-57
–
–
204
14,2
70-74
191
14,0
198
11,4
120-130
167
6,2
252
3,6
MgCa2,0
55-57
–
–
195
12,2
70-74
193
9,2
197
10,1
120-130
184
4,8
266
1,2
Table 1
:
Mechanical properties of tubes of MgCa-alloys*
* Container temperature is 380°C
Extrusion ratio
35
51
71
89
128
Logarithmic deformation
3.56
3.93
4.26
4.49
4.85
Outside diameter of tube (mm)
6.54
6.57
6.34
6.15
5.91
Wall thickness (mm)
1.05
0.72
0.50
0.43
0.28
Outflow velocity (m/min)
2.6
3.8
5.3
6.7
9.6
Table 2
:
Process parameters during the extrusion moulding with a different extrusion ratio
Part of tube* Billet temperature [°C]
340 360 380 400 420 Billet grain size
Middle
grain size [µm]
5-10 10-20 10-30 10-35 10-40
5-35
End
grain size [µm]
10-20 10-25 10-35 10-25 10-40
Table 3
:
Influence of the billet temperature on the grain size
* ‘Middle’ – the sample was extracted in the range of 35-40 per cent of the tube length at the tube beginning; ‘End’ in 5-10 per cent
before the tube end
Extrusion ratio
35
51
71
89
128 Billet grain size
Grain size [µm]
8-15 (up to 20)
10-20 10-30 7-25 4-10
5-35
Table 4
:
Influence of the extrusion ratio on the grain size*
* The samples were extracted in the range of 35-40 per cent of tube length at the tube beginning
Figure 6
:
Influence of billet temperature on the mechanical properties of tubes
Figure 7
:
Influence of extrusion ratio on the mechanical properties of tubes
In figure 8 and figure 9 the structure of billet and tube can be seen.
Tables 3 and 4 contain the corresponding grain sizes. The structures
of extruded billets are comparatively homogeneous.
With regard to figure 8 and table 3, an increase of the billet
temperature causes bigger grains. At lower billet temperatures of
approximately 340-370°C, the tube grain size decreases in contrast
to the initial structure. At higher billet temperatures the tube grain