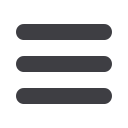

T
ube &
P
ipe
W
elding:
T
rends &
P
rogress
M
ay
2008
www.read-tpt.com116
›
Rofin, Germany, has launched StarPulse,
a new generation of pulsed YAG rod lasers
with power ratings ranging from 40 to
500W, which introduce a number of new
product technologies.
For laser welding of highly reflective
materials like copper or aluminium and
materials with high melting temperatures,
high pulse peak powers are required. The
StarPulse lasers provide high peak powers
up to 20kW. Welding of components with
high thermal conductivity can be achieved
with large welding depths and high process
speeds.
The control of the StarPulse lasers is
based on Rofin’s new RCU control unit.
The RCU achieves power control with
the Double Closed Loop
TM
method. The
double closed loop guarantees pulse-
to-pulse stability and intra-pulse control
independent of back reflections from the
workpiece.
With precisely controlled laser pulses down
to a few mJ of pulse energy, welding of
extremely thin wires (diameters down to
50
μ
m and smaller) used in the medical
device and electronics industry, or seam
welding of the finest thin-walled metal parts
is possible.
The Double Closed Loop allows optimal
adjustment of the so called Shadow
technology – a quasi cw-welding – to the
user’s process. The entire weld seam is
produced by a single laser pulse at a high
feed rate.
The benefits of this method, which is
particularly suitable for micro and fine
mechanics products, are reduced thermal
strain and higher process stability,
compared to spot welding.
The graphical display of the measured pulse
on the Real Time Application Monitor™
allows online control of each pulse. This
feature is beneficial for processing alloys
New generation of pulsed YAG lasers
Simple and efficient operation via touch panel
StarPulse provides welding via pulse-to-pulse
stability