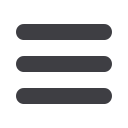

73
M
ay
2008
www.read-tpt.comT
echnology
U
pdate
›
machine is cutting the piece, it can load
the next tube or unload the previous one.
This means that loading and unloading
operations do not influence cutting time.
The plant, equipped with a 4kW resonator,
is also able to make a marking which allows
tracking of the produced parts, optimising
the logistic management of the finished
parts.
Tube Tech Machinery
– Italy
Fax
: +39 030 7256 333
:
info@tubetechmachinery.comWebsite
:
www.tubetechmachinery.comSeamless tube mill
modernisation
The Russian TMK-Group, one of the
world’s largest oil and gas pipe producers,
has placed an order with the Italian
Danieli-Group for the modernisation of
the seamless tube mill at its subsidiary
Seversky Truboprokatny Zavod (STZ).
With Danieli Centro Tube (DCT) being
the main contractor, the pilger mill will be
converted into a continuous 14" seamless
tube mill with an annual capacity of 600,000
tons, and will simultaneously be radically
modernised.
A 5-stand retained mandrel mill FQM™,
a 3-stand extracting mill, and a new
14-stand sizing mill will replace the
previously operated two pilger mills and
the two subsequent sizing mills. Most of
the downstream machinery will also be
replaced.
According to the cooperation agreement
between DCT and Friedrich Kocks
GmbH & Co KG, the company will again
be responsible for the process, design,
supply and commissioning of the 3-stand
extractor and the 14-stand sizing mill. Both
mills are equipped with the innovative Star
Drive, featuring individual drives for every
roll.
The 3-roll stands are designed for a
nominal roll diameter of 650mm. The
extractor operates with non-adjustable
stands only, whereas the sizing mill has
both non-adjustable and adjustable stand
types.
Important characteristics are the quick
stand changing system, the inline remote
controlled pass adjustment for the adjustable
stands, and the quick roll changing system
in the roll shop.
After conversion, the new mill will produce
seamless tubes with diameters ranging
from 168 to 365mm OD and wall thickness
of 6.28 to 37.3mm, with excellent tolerances
and material characteristics in accordance
with the international standards to be used
in the oil and gas industry. The new mill is
scheduled for start-up in 2010.
Friedrich Kocks GmbH & Co KG
–
Germany
Fax
: +49 2103 54 028
:
v.d.heiden@kocks.deWebsite
:
www.kocks.deTMK-Group
– Russia
:
tmk@tmk-group.comWebsite
:
www.tmk-group.comDanieli
– Italy
Fax
: +39 02 262451
:
r.giannattasio@danieli.itWebsite
:
www.danieli.comn
❖