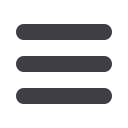

and reducing maintenance.
However, a truly contactless connector
must be able to transmit both data
and power. For power, there are few
options. Capacitive power transfer
(CPT) has the advantage of being
able to penetrate (floating) metal and
has low EMI, but it suffers from low
power density and short range. Some
generalized comparisons of various
wireless options, using pros and
cons, are shown for easy reference
(Figure 1.)
For contactless power transfer, an
inductively coupled power transfer
(ICPT) option proves to have more
pros than cons. It is has high power
density at reasonable distance, is well
known with widely available product
and technology solutions, and high
efficiency is possible. The downside
is that it cannot penetrate metal.
For data transmission, there are
a number of options. Capacitive
coupling’s low EMI is also an
advantage for data transfer, but such
coupling requires significant surface-
plate area, which can be challenging
for tiny, rotating couplers. Inductive
coupling for data suffers from low
bit rates. Other options include RF
at 60 GHz, 2.45 or 5 GHz, sub-GHz,
and ICPT, as well as optical links.
Each has pros and cons, as shown in
Figure 1.
The 2.45-GHz industrial, scientific,
medical (ISM) band is also unlicensed,
with global acceptance and wide
usage, most notably as “wireless
Ethernet” under the moniker of Wi-
Fi.
In the final analysis, it turns out that
a hybrid architecture, RF for data
and inductive coupling for power,
is the best approach for contactless
connectivity.
Defining induction
Inductive power transfer has been
with us for quite some time, but
for the sake of clarity a quick run
Figure 2. In inductive coupling, the coupling is determined by
the distance (z) and the ratio of D2/D, while the efficiency of
power transfer between transmitting coil L1 and receiver coil L2
depends on the coupling (k) between the inductors and their Q
factor
design criteria that need to be
considered for each application.
The ability to transmit over “certain
distances” as mentioned above is
particularly interesting. There are
instances where power and data
need to be transferred wirelessly
across small distances, such as
through a wall or other material.
Also, more connector freedom may
be needed without mechanical wear
and tear, or the environment may
be too hazardous to introduce any
possibility of arcing.
It’s at this point that advances in
contactless connectivity need to be
considered.
Contactless connectivity
“Contactless connectivity requires
both contactless power and
contactless data technology which
can easily connect over a short
distance without physical contact”
[TE Connectivity (TE)].
There are many benefits to be
accrued from contactless over
traditional connectors which should
be considered when deciding how to
meet the design specification most
effectively. These include:
Improved reliability:
Delivers
robust power and data without wires
or physical contact. Also, the
connectors are hermetically sealed
ensuring environmental integrity.
Greater flexibility:
There is an
unlimited range of motion, allowing
360° movement, tilt, angle and
misalignment.
Unlimited mating cycles:
There are unlimited mating cycles in
wet and dusty environments. This is
particularly suitable where slip rings
or spring cables reach their limit.
Connection through walls or
materials:
Contactless technology
allows connection through walls or
materials, which is not possible with
traditional connectors.
Improved safety:
There is no
arcing, which is a major plus in
hazardous environments such as
gas-filled chambers.
Cost savings:
There is no wear
and tear thus improving the uptime
Sensors
Special Edition
New-Tech Magazine Europe l 55