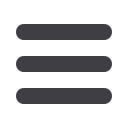

66
J
uly
/A
ugust
2007
straightening machine generation is based
on in-depth experience and a continuous
exchange with tube mills.
Common problems such as hooked ends
and tube end deformation are avoided due
to the special roll profiles and a combination
of hydraulic clamping and cylinder systems.
The yield of the mill and the material scrap
losses can therefore be efficiently reduced.
The high accuracy in straightness is
achieved by a special combination of
bending and ovalisation of the tubes
between the rolls. The tubes are plasticised
in a multi-stress combination with a
wide contact zone in between the rolls.
The hydraulic locking elements of the
roll columns are concentric and wear-
free, therefore the angular and vertical
adjustment of the rolls is precise and
repeatable.
Reika GmbH & Co KG
– Germany
Fax
: +49 2331 969 036
:
info@reika.deWebsite
:
www.reika.deReika, Germany, has achieved a great deal
of success with its new generation of multi-
roll straightening machines.
Several machines have been sold to
leading German and East European tube
mills working in various diameter ranges.
The machines are available for all kinds of
seamless and ERW tubes up to 24".
The company has also developed special
straightening machines for hot tubes
being processed in heat treatment lines.
In particular, OCTG pipes with high
yield strength require this hot
straightening operation.
The machines are designed with
state-of-the-art 3D CAD systems
and offer finite element optimised
frames and high rigidity. The
straightening machines can be
supplied with individual drives
for roll wear compensation and
dynamic process control.
Machines are set automatically with
execution of proven mathematical
and empirical algorithms, leading
to short setup times and repeatable
straightness qualities. This new
S
traightening &
F
inishing
T
echnology
A
ccording to the prolific commentator
Anonymous, it’s not over till it’s over. Thus
last-minute losses are a fact of life. The horse
stumbles. The front-runner fades. A defender
comes out of nowhere to clear off the line. In
tube and pipe production, straightening and
finishing operate at that stage. They do not
make the product, but they can break it.
Suppliers of straightening and finishing
technology to tube makers must have a highly
cultivated sense of ‘just right’. Too much
pressure, tension, torque, speed, angulation,
or force, and material turns to scrap; too little, and the procedure has to be repeated. Now, as ever, time is
money. It is also – in an impatient world in which a reputation can be indelibly marked by a late shipment
– productivity and profitability.
At a certain point in time, a hands-on designer realises that a belt-width smaller than the one in a
‘straight
only’
polisher/grinder allows the sanding belt to follow around a curve. The unit, already dual-purpose,
gains capability to accept straight, curved, and bent tubes of any ferrous metal. In its next generation
it will offer capability for grinding, cleaning, smoothing, and polishing conical, oval, and other complex
parts, in many more materials.
This review discloses that kind of progression in straightening and finishing: a steady expansion of the
province of
‘the new normal’
from specialists at a make-or-break station in tube production.
Specialised tube straightening machines for heat treatment lines
fi
Reika’s tube straightening technology for ERW tubes up
to 24"