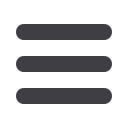

S
traightening &
F
inishing
T
echnology
68
J
uly
/A
ugust
2007
better fittings:
from a leading manufacturer. Proven
and used throughout the world. ERNE buttwelding
fittings are made of alloyed and unalloyed steels,
stainless steel and further materials.
best connections:
that means product availability,
rapid response times and reliability in quality and
delivery. Outstanding logistical capabilities and
excellent service make ERNE FITTINGS a flexible
partner for stockists/distributors and project
specialists the world over.
better fittings. best connections.
erne
fittings
erne fittings gmbh,
A-6824 Schlins, Hauptstrasse 48,
Austria/Europe,
office@ernefittings.com www.ernefittings.comKeetons, UK, has recently installed and
completed startup of a new tube boring
machine. With a 1,200mm diameter chuck,
it is the largest of the company’s 4 tube
boring machines.
The machine is able to bore thick walled
tubular components from 2-10m in length,
with bores from 60mm to over 600mm
diameter. The machine also has a 500mm
diameter hollow spindle to handle extra
long jobs.
Delivery of this machine follows
numerous other developments including
the introduction of a second 8m honing
machine.
One of the company’s deep hole boring
machines used for boring solid bars and
forgings has also met with success.
The machine can bore jobs up to 6.5m
long, but has a 4m-bed extension planned
to increase the number of machines with
capacity of over 10m.
Keetons has been producing and
processing thick walled tubular components
from seamless tube and solid bar for over
80 years. Despite recently increasing
capacity and although boring jobs over
1,000mm long are normally undertaken, the
company can also machine smaller items.
The company’s smallest borer can handle
bores of 20-70mm diameter from solid bar
in lengths of up to 4m.
Keetons
– UK
Fax
: +44 114 243 5348
:
enquiries@keetons.comWebsite
:
www.keetons.comComplete finishing centre
brings advanced
tube production
OAO Pervouralsky Novotrubny Works, part
of the ChTPZ Group, Russia, has placed
an order with SMS Meer for the supply of
a complete finishing centre for its existing
pipe plant.
The finishing centre is designed for an
annual capacity of 75,000 to 90,000t and
consists of a tubing/casing line, testing line,
upsetting line and heat treatment unit.
The whole complex is coordinated and
controlled by a superordinate computer
system. Tubes in the size range from 60.3
to 177.8mm can be finished on the tubing/
casing line.
The line essentially comprises four
pipe threading machines, a two-head
hydrostatic pipe tester with a maximum
pressure of 150MPa, two drifter units for
checking the pipe inside diameter, and the
automatic measuring system (weighing,
length measurement, testing and marking).
Also included in the line is a magnetic
bundler for stacking pipes in hexagonal
bundles.
On the upsetting line, tubing and drill pipes
in the size range from 60.3 to 127mm are
upset at the pipe ends.
The scope of supply includes an
upsetting press with an upsetting force
of 2,500kN, with upline induction heater
and the necessary inspection and testing
stations.
The testing line is used to inspect the
quality of the heat treated and non-heat
treated pipes.
Longitudinal and transverse flaw tests are
performed in accordance with international
standards. Upset and plain-end pipes in the
size range from 60.3 to 219.1mm are heat
treated on the heat treatment line.
The scope of supply includes a hardening
furnace and an annealing furnace (supplied
by an Italian subsidiary of SMS Meer),
quenching facilities with the associated
water management system, a hot
straightener with the necessary contraflow
cooling beds, and the interconnecting
transport facilities.
With this new finishing centre, the
Pervouralsky Novotrubny Works pipe mill
is now in a position to produce pipes of the
highest grades and qualities.
Commissioning of the whole finishing
centres is scheduled for the end of 2008.
SMS Meer
– Germany
Fax
: +49 2161 350 862
:
info@sms-meer.comWebsite
:
www.sms-meer.comLarge tube borer boosts production
›
The boring of 475mm x 9m thick walled tubes
used for the international energy market