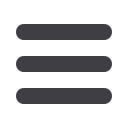

86
J
uly
/A
ugust
2007
There was a time, and not so very long ago, when
the word ‘plastic’ did not appear in a publication such
as
Tube & Pipe Technology
. Old-timers will recall
an early problem with the dubious new material:
was the preferred adjective ‘plastic’ or ‘plastics’?
It seemed unlikely that the subject of such effete
reflections would find a place in an industry with
its roots in iron and steel. Moreover, the new
technology was promising the moon. Makers of
tube and pipe know how to greet large claims for
untested new products: with profound skepticism.
But the proof was not long in coming, and it was
solid. Applications incorporating the new plastics enabled tube and pipe producers to promise value-
added performance. These producers were also able to deliver efficient heat exchange characteristics,
cross-contamination resistance, robustness to a wide range of chemicals and temperatures from -40¼ºC
to 120¼ºC, and much more.
The inert nature of PVDF, PP, and HDPE thermoplastics ushered the producers to places – particularly
in the chemical, pharmaceutical, and electronics industries – well outside their traditional territory. In fact,
the use of plastics and composites in tube and pipe manufacture has come very close to giving them the
moon.
Today, there are no sceptics in the industry.
Consisting of plastic and metal, multilayer
pipe systems offer advantages of high
resistance to internal pressure (especially
at high temperatures), innovative and
economical fitting technologies and easy
mounting.
In general, multilayer pipes and fittings of
different systems cannot be interchanged
due to the large number of design varieties.
Therefore it is important to test pipe and
fitting systems very thoroughly before
installation, especially as metal and
plastic have different thermal coefficients
of expansion. If the temperature differs
substantially, as for example in drinking
water installations, tightness and durability
of these systems can be crucial properties.
SKZ is an accredited institute for testing
according to DIN EN ISO/IEC 17025 and
an accredited inspection body according to
DIN EN ISO/IEC 17020.
The company provides mechanical testing
devices required for certification and quality
assurance of pipe systems meeting national
and international specifications.
SKZ operates as a testing laboratory and
inspection body for systems used in drinking
water installation on behalf of DVGW in
Bonn, Germany. In the field of floor heating
systems SKZ cooperates with the certifier
DIN Certo of Berlin, Germany. In addition,
SKZ is its own certifier for products marked
with the reputable SKZ-sign.
Typical tests on multilayer pipe systems
executed by SKZ are long-term hydrostatic
pressure tests at different temperatures,
together with dip thermal cycling tests.
Here adhesion from plastic medium pipe
and aluminium pipe is tested after a long-
term thermal cyclic load.
Within 15 minutes, the pipe is loaded with
cold water at 20°C and with hot water at
93°C at 10 bar internal pressure. This
cycle is repeated 5,000 times, which takes
about 105 days. Following this process,
the minimum adhesive strength is tested
during a so-called separation test (see
picture above).
Süddeutsches Kunststoff-Zentrum
(SKZ)
– Germany
Fax
: +49 931 4104 277
:
j.wuest@skz.deWebsite
:
www.skz.deP
lastic &
C
omposite
T
ube:
P
roducts &
M
anufacture
Testing of plastic-metal multilayer pipe systems
›
Aluminium layer peeled off plastic medium pipe