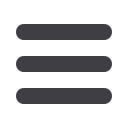

88
J
uly
/A
ugust
2007
P
lastic &
C
omposite
T
ube
Wayne Machine & Die Company, USA,
has launched a new Yellow Jacket vertical
extruder series. This series is unlike typical
vertical extruders with inline gearboxes
that have all the weight of the mechanical
section on one side of the post.
Instead, the motor is positioned on the
opposite side of the extrusion processing
section, resulting in a more balanced weight
distribution. This helps to prevent ‘tip overs’ –
a major safety problem with vertical extruders.
The design also allows the use of double
reduction helical gearboxes with shaved
ground and hardened gears. These are an
alternative to the often inefficient soft gear
worm or enveloping worm-type gearboxes
that are typically found on direct drive
vertical extruders.
The helical gearbox enables delivery of
more power to the screw, less wasted
energy converted into heat from friction,
and less abrasive gear wear than is found
in worm drives.
Processors are able to run engineering
and highly filled resins in coextrusion
applications, which require high levels of
screw torque. The extruders also process
PE, PVC, EVOH, PP, TPR, silicone, rubber,
food and most thermoplastics. A high
temperature/anticorrosive package is also
available for Teflon FEP, Saran, ETFE, PFA
and liquid crystal polymers.
The new single-post series is available in
½",
5
/
8
", ¾", 1", 1¼", and 1½" sizes, while
the double post machines are designed for
2" and 2.5" sizes. The units feature timing
belts for easy speed range changeovers,
AC flux vector drive, auto-tune temperature
controls, bimetallic barrels and optional
remote stations.
Suitable for coextrusion of sheet, tubing,
profile, rod, blown film, cast film, fibre,
The Prandelli Plus system, from Prandelli
SpA, Italy, consists of a PE-Xb/AL/PE-Xb
composite pipe and dezincification-resistant
brass connectors. Connections are made
using an axial sliding operation.
During the manufacture of Prandelli Plus
pipe the inner core is covered lengthwise
with butt-welded aluminium foil. The fluid
runs through this inner core, with full
compliance with PE-X pipe standards. The
aluminium is then covered with a further
layer of cross-linked polyethylene (PE-Xb).
Due to the size of the pipe, the finished
product has high mechanical and thermal
resistance, making it suitable for both
heating and sanitary systems, the latter
often being under stress. Important
characteristics of Prandelli Plus pipe
include corrosion proofing, smooth and
even surface, thermal conductivity, low
noise, and a barrier to oxygen.
Prandelli Plus has been designed to safely
withstand any stress that may occur within
hydraulic, heating and sanitary systems.
The tube can be classified as PN16,
meaning it can withstand a pressure of
16 bar at a temperature of 20°C for a
continuous operation period of 50 years.
The tube can work constantly at a
running temperature of 60-70°C. It can
withstand temperatures of up to 80°C and
malfunction temperatures of the hot water
generator or control systems of up to 95°C.
For applications in panel heating systems,
the maximum temperature is 90°C and
the malfunction temperature is 100°C, as
provided for by the specific UNI EN ISO
15875-1 regulations.
Prandelli SpA
– Italy
Fax
: +39 0308 921739
:
prandelli@prandelli.comWebsite
:
www.prandelli.comPipe for heating and sanitary systems
fi
The Prandelli Plus system uses PE-Xb/AL/PE-Xb
composite pipe and brass connectors
New ‘Yellow Jacket’ vertical extruders for coextrusion