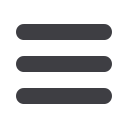

Cutting
www.read-tpt.comJ
anuary
2014
89
Vertical bandsaw for
valve manufacturer
BEL Valves, based in Newcastle, UK, is
a designer and manufacturer of critical
oil and gas valves for both surface and
subsea applications, serving evolving
markets that demand the highest quality
and reliability. The company has around
50,000 valves installed worldwide, some
of which operate in the most inhospitable
environments on the planet, often in
ultra-deep waters of up to 10,000ft,
under high pressures and extremes of
temperature.
With valve sizes ranging up to 48" in
diameter and tolerances typically less
than one micron, precision machining
is of the utmost importance. When
BEL Valves needed to upgrade
the cutting operation during the
production of 24" diameter split gate
4A topside through-conduit valves,
it turned to Prosaw to provide the
solution.
Although the existing process
utilised a vertical bandsaw, it was
very wasteful of material, typically
deviating from its true path by up
to ½" on either side of the blade,
requiring a considerable amount
of post-cutting additional machining in
order to form a true surface.
Prosaw specified a
Danobat
VL
vertical
bandsaw,
which
has
reduced the cutting time for
the product from 18 hours
to just six hours. The more
accurate cutting path has
reduced waste material,
and the company reports
that this amounts to cost
savings in the region of
£1,500 for each valve.
Further cost savings
have been achieved by the
use of a new type of carbide saw blade
that has a life of more than 50 times that
of the previous machine.
Danobat
– Spain
Website:
www.danobatgroup.comProsaw
– UK
Fax: +44 1536 410080
Email:
sales@prosaw.co.ukWebsite:
www.prosaw.co.ukBEL Valves
– UK
Fax: +44 191 276 3244
Email:
enquiry@belvalves.comWebsite:
www.belvalves.co.ukA Danobat bandsaw with the workpiece in place
The cutting edge
Multi-functional tooling system
GUEHRING offers over-turning, internal
and external chamfering of tubes and
bars in a single operation.
The flexibility of its modular tooling
solution maintains the transformation of
the standard tool GE 100 into a “special
tool” for the most varying of machining
tasks and this ex-stock.
The standardised modular system
succeeds through its adaptability to
different diameters, materials and
demands on precision. Thanks to its
flexibility, machining diameters from 5 to
240mm are possible with GE 100. The
tool head can be universally applied: it
allows adaption to all known machine
holders, including all quick-change
systems. By exchanging the holder or
clamping sleeve it is possible to machine
different workpieces with one basic
holder, ie tool head. The bore in the tool
head serves as clamping sleeve holder
for centre drills, step drills, form drills
or boring bars. The adjustment of the
radially and axially moveable holders is
simply carried out via a threaded pin.
The standard DIN/ISO insert
programme for the holders is
specifically adapted to the GE 100 user
requirements. The indexable inserts are
high-precision ground, enabling optimal
component accuracy, repeat accuracy,
low cutting forces and therefore high
process reliability.
Ground chip breaking grooves
produce short chips that are absolutely
essential for accurate machining with
multiple inserts. The insert programme
includes various carbide qualities as well
as diverse coatings enabling optimal
tool life, cutting rates and low unit costs.
Various machining tasks such as
facing, external and internal chamfering,
spot facing and centring or over-
turning can be combined. Alongside
the application on end machining
systems GE 100 also achieves efficient
machining strategies on machining
centres or rotary indexing machines.
Guehring
– Germany
Website:
www.guehring.deGuehring tube chamfering technology