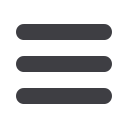

Cutting
www.read-tpt.com84
J
anuary
2014
High strength circular saw blades
NEW-FORM Tools offers specialist
blades and cutting systems for high
tensile and high strength materials. For
over 30 years it has been manufacturing
metal cutting solutions for the tube
and pipe, roll form and coil processing
industries.
New-Form Tools titanium coated
shear blades, jaws and roll-forming tools
are impact and wear resistant. With
durable tooling that resists chipping and
cracking, New-Form Tools is a good
source for cutting solutions.
The company offers its range of
cutting blades across North and South
America for durable, high-speed steel
and specialist high-speed steel circular
saw blades.
Jim Jantzi, president of New-Form
Tools, said: “We knew expanding our
product line was the right decision.
There is such a high demand in North
and South America for high quality,
long-lasting, circular saw blades and
we knew this was a decision that our
existing customers could also utilise
for their operations. We’re more than
thrilled to say that we now serve the
whole tube cutting market.”
From the manufacturing process to
regrinding and custom design, New-
Form Tools said it is proud to supply
operations across the world with its
cost effective, high quality circular saw
blades.
New-Form Tools
– Canada
Email:
tjantzi@newformtools.comWebsite:
www.newformtools.comMulti-cut tube cut-off machine
THE stationary tube cut-off machines
multi cut (MC3) is a new machine
from Linsinger that revolutionises tube
cutting with diameters between 150
and 660mm. Instead of one large saw
blade, it has three smaller circular saws
attached to a radial rotating disc and
gives a clean ready-to-sell cut.
Much shorter cycle times result from
the simultaneous intervention of all
three saws in the tube and subsequent
rotation by 120°; the actual cutting time
for a P110 steel tube in the size 244 x
13.5mm is therefore only eight seconds.
Another decisive advantage: if one of
the saws fails, the machine can continue
processing with slightly less power but
without interruption up until scheduled
replacement of the saw blades. This
avoids expensive production stoppages.
According to Linsinger, the efficiency
of the MC3 is unrivalled due to several
reasons: in contrast to the large
and therefore expensive blades in
conventional steel circular saws, much
smaller and correspondingly less
expensive disposable saw blades can be
used in the Multi Cut machine. Together
with the construction-related higher life
time of smaller saw blades, this is a
massive reduction in tool costs, which
are often higher than the cost of the
actual machine
for circular saws
that
may
be
used for more
than 20 years.
Beyond that the
thin cutting width
saves a lot of
material.
Last but not
least, the MC3
impresses
with
the fully automatic
tool change per-
formed by a robot
as soon as a certain number of cuts has
been achieved. It changes all three saw
blades in just 90 seconds – this would
be a pit stop in record time in Formula
One.
In relation to a twenty-year life cycle of
the machine, the time savings achieved
corresponds with more than half a year
in three shift operation.
“The MC3 is not only the measure
with all things in precision but also in
the efficiency of the machine. The extra
cost in comparison to conventional
saws amortises within two to three
years.”
This is how the Linsinger company
manager Hans Knoll summarises the
number of advantages, which also
convinced several customers. And not
only them: “The benefits of our multi-
cut system have also already been
recognised in China. We are expecting
a run on this new machine type from the
local industry,” explains sales manager
Johann Wolfschwenger.
For further information visit Linsinger
at Tube Düsseldorf Hall 6, Stand 6K20.
Linsinger
– Austria
Email:
maschinenbau@linsinger.comWebsite:
www.linsinger.comYoder upgrades WH-350 tube mill
YODER Manufacturing of Cleveland,
Ohio, a member of the Formtek Group,
has been contracted to refurbish and
upgrade an existing WH-350 tube mill to
produce structural shapes (HSS).
Formtek is a group of long-established
companies, eachwith awell-known name
and a history of providing innovative,
reliable equipment to the metal forming
and metal processing industries. As a
single source provider, Formtek supplies
all of its customers needs.
Formtek
– USA
Website:
www.formtekgroup.comMulti-Cut MC3-406 in operation in Brazil