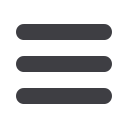

Cutting
www.read-tpt.comJ
anuary
2014
83
Specialist tube machines
SMS Engineering is an Italian
engineering and manufacturing com-
pany that specialises in tube machinery.
Itsmachinesperformfinishingoperations
on metallic tubes by making use of
simple hydraulic units, similar to small
presses, which are linked to a hydraulic
power pack and duly positioned on a
steel surface (being a rig or a plate) and
can punch, flatten, swage (reduction of
the tube ends) and cut the tube.
The tube and all its machining
cover a wide range of uses and can
be found in baby articles production
(perambulators,
push
chairs,
school desks), home appliances
(clothing driers, domestic ladders,
heaters, radiators), building production
(scaffolding), automotive production
(car safety bars, seat adjusting levers,
head rests), leisure time (swings,
deckchairs,
camper
accessories,
tents), garden items (grass cutters,
wheelbarrows), and furniture (chairs,
shelves and office furniture).
The machine working is provided
through the manual feeding of the tube,
which is closed by the gripper, and then
by pressing the start cycle. The machine
makes all the operations and the finished
tube comes back to the starting point
where it is unloaded. Using this machine
you can work bars of length 3m with the
possibility of cutting the tube.
Options available include ordering
the machine with automatic loading/
unloading and with the possibility of
working commercial bar length of up
to 6m. The machine can work up to
ø120mm round tubes and square/
rectangular tubes maximum 80x80mm,
with or without deformation in steel,
stainless steel and aluminium.
The machine is accurate as a
laser machine but it requires lower
investment. The best advantage of
the plasma machine as regard to the
traditional punching machine is that you
can program it and avoid in this way the
exchange operation of the toolings and
corresponding costs for each different
mould: different shapes of holes and
hole-slots can be performed on the
same tube.
The plasma cutting machine is also
very easy to use. In order to program
it, you must be acquainted with the
CAD-CAM systems and just a short
period of training is enough to become
confident. The machine is suitable for
manufacturers of shelving, radiators,
stairs, bed nets, ladders, parts for cars,
furniture and similar tube products for
different sectors.
SMS Engineering
– Italy
Email:
commerciale@sms-italy.itWebsite:
www.sms-italy.itEfficient in-line cutting
KINKELDER has developed a smooth
cutting TubeMaster
®
saw blade for
orbital cut off applications. Its special
tooth-geometry cuts a large range of
thin- to thick-wall tubes.
“Key features of this TubeMaster saw
blade are a special carbide grade and a
high-tech PVD-coating,” said Kinkelder
application engineer Leo Molenaar.
“This, combined with a special cutting
geometry, does not require much force
for chip removal, assuring a milled-like
finish of the cut surface. This special
geometry also reduces vibration when
cutting thin wall (<4mm) tubing, thereby
achieving an excellent blade life.”
The saw blade concept allows the use
of one set of blades with medium tooth
pitch to cut tubes with wall thickness from
3 to 9mm, and on some machines even
up to 12mm. For wall thickness from 9 to
30mm, a coarse pitch is defined.
TubeMaster saw blades are available
in diameters from 300 to 420mm for all
types of orbital cutting machines.
Tubes for oil and gas, as well as
structural pipes and hollow sections,
form a primary market for TubeMaster
saw blades. Even high hardness
materials such as X80 can be cut
efficiently thanks to the type of carbide
used.
The PVD coating protects the
tips against the high temperatures
developed during the cutting process.
In the case of ID scarfing in the tube
making process, the internal weld bead,
often around 6mm thick solid steel,
remains inside the tube. During cut-off
this inside wire is caught by the saw,
causing a huge peak load, usually on
one saw tooth. This can lead to tooth
breakage of the saw blade.
Kinkelder started developing a new
saw in 2010, which resulted in the
ScarfMaster
®
– a carbide-tipped saw
blade featuring a very specific tooth
geometry, with the tips themselves being
made of a highly shock resistant type of
carbide. The teeth are supported by a
saw body with extra strong shoulders,
which give the combination tooth/
body very high stability and fracture
resistance.
“Not only is the blade life of the new
ScarfMaster considerably longer, it can
also cut 50 per cent faster,” emphasised
Mr Molenaar. “Due to this, line speed
can be significantly increased. Also, the
line does not have to be shut down as
often to change the saw blades, which
means better uptime.”
Kinkelder BV
– Netherlands
Fax: +31 316 58 22 17
Email:
info@kinkelder.nlWebsite:
www.kinkelder.comA Kinkelder saw blade