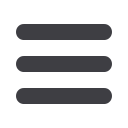

labs are booked up several weeks
out. However, small blocks of time
for preliminary testing typically can
be found outside of peak hours.
The small amount of resources
spent performing preliminary EMC
testing early in the design cycle may
prevent considerable and expensive
redesign efforts late in the product
schedule.
Another common reason for
delaying the EMC testing of a system
is the misconception that the power
supply causes the EMC issues and
thus a system will pass testing if the
supply has already passed stand-
alone regulatory testing. In many
instances, the power supply is the
recipient of the blame for EMC
issues within the system when in
reality it is ‘only the messenger’.
While system conducted and
radiated EMC issues are often
addressed at the end of a project,
that phase in the schedule is
perhaps the worst time to introduce
unexpected tasks and delays. Amore
reasonable and often lower cost
strategy is to perform preliminary
EMC compliance testing as soon as
the system assembly has begun.
Earlier in a project, schedules are
more flexible and design teams are
more receptive to modifications in
the design.
By the end of a project much effort
has been applied to designing
the system to meet performance
criteria and if an EMC compliance
issue arises the power supply is
perceived as the easiest target
for compliance efforts without
affecting other system performance
parameters. Although the system is
often the source of RF emissions,
the cabling on the input and the
output of the power supply may
be serving as antennas for radiated
emissions and conductors for
conducted emissions. It is often
possible to add noise suppression
components to the power supply
to address the EMC issues, but this
activity should be recognized as
mitigating the effects of the problem
and not addressing the source of
the problem. The EMC suppression
activities associated with the power
supply require time from the design
team and may affect the safety
certificates associated with the
power supply. Any changes to the
safety certificates will also require
time and resources from the power
supply vendor. The system circuitry
may need to be modified to minimize
the generation of RF signals if
adding conducted and radiated
emission suppression components
are insufficient to adequately
reduce the EMC problems.
For products which use internal
power supplies, EMC noise
suppression components can be
added either on the conductors
feeding into the power supply
or on the cabling between the
output of the power supply and the
power input to the system. Bypass
capacitors and ferrite cores are
suppression components used to
create filters to address EMC issues.
Ferrite cores introduce additional
inductive impedance in series with
the path of the unintended noise
and bypass capacitors provide
a low impedance path to shunt
noise signals to minimize signal
propagation.
Systems employing external power
supplies may be more limited in
their ability to add EMC suppression
components on the input or output
paths of the power supply. Radiated
emissions issues are typically
addressed with a ferrite core
placed on the cable between the
power supply and the system. The
frequencies of concern associated
with conducted emissions are low
enough such that the size of a
ferrite core required to fit around a
power cord and mitigate EMC issues
will be unacceptable for many
applications. Conducted emission
issues observed in systems with
external power supplies are often
most easily addressed by working
with the power supply vendor to
modify the design of the existing
supply or selecting a different
external power supply incorporating
enhanced conducted emissions
suppression components.
Pre-Compliance Testing
Final testing of conducted and
radiated emissions needs to be
performed in a certified laboratory
using calibrated test equipment and
a controlled electrical environment.
Testing labs will cooperate to
perform pre-compliance testing
early in the design phase. If the
design team desires to conduct the
Figure 2:
Conducted emissions filter components
64 l New-Tech Magazine Europe