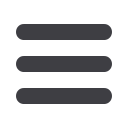

18
SAIW Member profile: Hydra-Arc
AFRICAN FUSION
November 2015
Low str ss no distortion welding
extraction and to minimise interference with the welding arc
and weld pool.
Thermocouples were attached to the underside plate
material, positioned at 7.5, 15 and 20 mm from the weld
centreline, and bead-on-plate tests conducted. By attaching
the thermocouples to the underside of the plate they were
protected from being ripped off by the cooling head or direct
impingement of the CO
2
.
The welding trials were carried out with and without
cooling, using the cooling arrangement shown in Figure 1
and 2. Sample results from the thermocouple study can be
seen in Figure 4, which shows the effect of the cooling on the
temperature profiles.
Further, a comparison of weld macro sections shows that
thewelds fromboth conventional and LSND processes exhibit
similar cross sectional shapes, beadwidths andheights, aswell
as comparable levels of penetration. The two macro sections
can be seen in Figure 5.
Representative sampleswere thenmeasured for distortion
using a Faro arm measurement system and macro sections
taken to reviewweld quality. Typical sample distortion results
for the bead on plate specimens are illustrated in Figure 6,
which clearly show that a reduction in distortion of between
40-50% is achievable with the system in the trial. The typical
results for bead on plate samples are illustrated as a simple
visual side-by-side comparison as shown in Figure 7.
The microstructure examination of samples from both
weldmethods showed the resultingmicrostructure to be very
similar. And when the micro-hardness was also checked by
traverses across typical samplewelds, the results fromsimilar
populations where not significantly different.
Once a reliable system was established, the trials were
repeated using simplified ‘real’ joint conditions using the robot
mounted DC-LSND welding system. Trials were carried out on
butt welds in 2.0 and 2.5 mm thicknesses in XF350 steel plates,
andon a ‘tophat’ section in 2.5mmsteel, withboth 2.0mmand
2.5 mm closer plates; this condition being chosen as it is repre-
sentativeofmanyoftheweldjointsusedinautomotiveproducts.
Figure 4: Temperature plots for 2.5 mmmaterial welded at 650 mm/min using
the robotic LSND system: (a) conventional (top graph), without cooling active;
and (b) cooled (lower graph) using the DC-LSND with CO
2
snow.
Figure 5: A comparison of macro section results for conventional
GMAW weld (top); and the LSND process weld (below) for typical
bead on plate sample welds.
Figure 6: A comparison of the out of plane distortion measurements
in typical sample welds.
Figure 7: A visual comparison of distortion in typical sample bead on
plate welds.
Representative sampleswere thenmeasured for distortion
andmacro sections taken to reviewweldquality. It canbe seen
in Figure 8 that themacro section from the LSNDweld exhibits