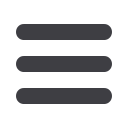

November 2015
AFRICAN FUSION
23
References
[1] The Lincoln Electric Co. Cleveland, Ohio USA: “Prevention and
control of weld distortion”, Weld J (2001), page 97–100.
[2] CJHamelin and L Edwards: “Reviewof DistortionControl Tech-
niques for Welding Applications in the Shipbuilding Industry”,
ANSTO (2010).
[3] RW O’Brien: “Predicting weld distortion in the design of auto-
motive components”, MSc Thesis, Durham University (2007).
[4] Q Guan, CX Zhang and DL Guo: “Dynamically controlled low
stress no distortion welding method and its facility”, Chinese
patent no. 93101690.8., (1993).
[5] EM van der Aa: “Local Cooling During Welding: Prediction and
Control of Residual Stresses and Buckling Distortion”, PhD
Thesis, Delft University of Technology, (2007).
[6] DBertaso, G.Melton, RJones, andCHardy: “AdvancedManufac-
turing Using Low Stress No Distortion (LSND) Techniques”, IIW
Doc XII-1784-04, International Institute of Welding, IIWAnnual
Assembly, Osaka, Japan, (2004).
[7] QGuan, RHLeggatt andKWBrown: “Lowstress, non-distortion
(LSND) TIG welding of thin-walled structural elements”, The
Welding Institute (TWI) Research Report 374, (1988).
[8] DL. Guo, Q Guan and CQ Li: “New welding technique for aero-
space thin-walled structures-LSND technology”, in Proc of 18
th
ICAS, Congress, Vol. 2 (A93-14151 03-01), Sept. 20-25, Beijing,
China, (1992), page 1705-1711.
[9] J Gabzdyl, M Cole, SW Williams and D Price: “Control of Laser
Weld Distortion by Thermal Tensioning”, 20
th
International
Congress on ICALEO 2001: Applications of Lasers & Electro-
Optics Proceedings, USA, (2001).
[10] RV Preston: “Modelling of Residual Stresses in Welded Aero-
space Alloys”, PhD Thesis, University of Cambridge, (2001).
[11] DA Price, SW Williams, A Wescott, CJC Harrison, A Rezai, A
Steuwer, M Peel, P Staron and M Koçak: “Distortion control in
welding bymechanical tensioning”, Science and Technology of
Welding and Joining, Volume12 Issue 7, (2007), page 620-633.
[12] EMvander Aa, IMRichardsonandMJMHermans: “Weldingwith
a TrailingHeat Sink: How toOptimise the CoolingParameters?”
in ‘Trends in Welding Research’, Pine Mountain, Georgia USA,
ASM International, (2005).
[13] Y Ishizaki, S Asai, T.Tanabe, Y Yasuda and H Takebayashi: “De-
velopment of GTAW system using CO
2
cooling for reducing
residual stress”, IIW Doc # XII-1941-08, International Institute
of Welding, IIW Annual Assembly, Graz, Austria, (2008).
[14] R Holder, N Larkin, H Li, L. Kuzmikova, Z Pan and J Norrish:
“Development of a DC-LSND welding process for GMAW on
DH-36 Steel” in 56
th
WTIA annual conference (2011) page 1-13.
[15] NBagshaw, EOlden andDBersato: “Numerical Simulation and
Experimental Validation of Low Stress No Distortion (LSND)
Welding in 304 Stainless Steel”, The Welding Institute, United
Kingdom, Report 780/2003, (2003).
[16] N Bagshaw: “Low Stress No Distortion (LSND) Welding in 304
Stainless Steel: Improved Numerical Simulation and Experi-
mental Validation”, The Welding Institute, United Kingdom,
Report 813 /2004, (2004).
[17] R Saraswat: “LowStress NoDistortion (LSND) Modelling of Alu-
minium Alloy Welds”, The Welding Institute, United Kingdom,
Members Report 902/2008, (2008).
[18] RW O’Brien, WM Veldsman and GB Melton: “Weld cooling ap-
paratus andmethod using an expansible coolant and a refrac-
tory seal”, International Patent application WO/2012/101399,
International ApplicationNo: PCT/GB2012/000064, Publication
Date: 02.08.2012, International Filing Date: 24.01.2012, (2012).
Dual Wire 2.0 Power Clutch water-cooled Water Joint Water Joint Lite Frontpull 7 Power Clutch Wire Select 2.0 Power Joint Lite Frontpull 8i Lite Power Joint SKS torch solutions.