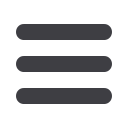

28
AFRICAN FUSION
November 2015
SAIW Member profile: Hydra-Arc
Fabrication for hygiene
I
ndustrial plants subject to health
and environmental regulations in-
clude food, dairy, pharmaceuticals,
cosmetics, andbeverage plants process-
ing drinks such as beer and wine, where
bacteria can be directly associated with
bio-film build-up on product-contact
surfaces. Tomeet the demand for great-
er plant hygiene, stainless steel plants
were built in the mid-1960s, which had
an intended life expectancy of 30 years
and more.
Hygienic processing plants are typi-
cally fabricated from polished 304L or
316L austenitic stainless steel, although
duplex stainless steels have recently
been introduced. In linewith regulations,
plant design philosophy requires: free
product flowwithout stagnation; protec-
tion fromthe external environment; and
cleanable plant interior surfaces.
When fabricating plants, standard
plates and pipes are formed and con-
nected together, often by welding, into
systems. Welding, an enabling tech-
nology, facilitates stress alignment of
components and thus lighter structures.
Whilst traditionally welding has always
focused on structural integrity, hygienic
welding introduces new challenges.
Fabrication for processing
Thesemay provemore demanding than
structural integrity, and are an addition
to other operational requirements in-
cluding environmental pressures.
Welded processing plants
Plants generally comprise a closed
system of tanks, heat exchangers,
mixers, distillation columns and inter-
connecting thin-walled pipes. Two par-
allel systems operate in tandem, one
product-related, and the second to fa-
cilitate cleaning of the internal surfaces
of pipes, vessels, equipment, filters and
fittings without disassembly, known as
clean-in-place (CIP). Up to the 1950s,
closed systems were disassembled and
cleanedmanually but with CIP, cleaning
is faster, less labour-intensive andmore
repeatable, posing less of a chemical
exposure risk to people.
The welded area in a plant is a very
small part of the total area of the instal-
lation. Fabrication and design detail,
however, influence plant performance
and cleaning processes, and can result
in lost productive time.
Realistically, hygienic welded fab-
rication will be both challenging and
costly. Although this puts capital bud-
Plants generally comprise a closed system of tanks, heat exchangers, mixers, distillation columns and
inter-connecting thin-walled pipes. Photo courtesy BOC and A&G Engineering.
In this article, Tony Paterson of the Wits School of Chemical and Metal-
lurgical Engineering describes the special welding requirements for
stainless steel piping in plant applications where bio-film build up on
pipe contact surfaces has to be avoided. Amathematical algorithmwas
developed to assess interconnecting pipes against the criteria of a point-
by-point minimum overlap of 80% around the pipe circumference.
gets under pressure, well-designed
and executed fabrication should ease
operational costs.
Factory and site welding
Whilst themajor components inprocess-
ing plants are factory built, many of the
small-bore pipe inter-connections are
made on site.
Factory conditions are easier to con-
trol as both sides of aweld are generally
accessible. During welding of products
accessible fromboth sides, protectionof
the tool side and the opposite side of the
weld by an inert gas is required to avoid
sensitisation. If carried out properly, the
need for post-weld treatments (grinding,
polishing, pickling and passivation) will
be minimised.
Site welding is more difficult as,
after fabrication, the system is closed
as access compromises sterility of the
equipment. The interiors of pipes are
only accessible to fabricators for clean-
ing, gas purging and NDT inspection
purposes. On-site welding is inherently
more difficult to control, more difficult
to monitor and more difficult to repair.
Inadequate welded joints compro-
mise product quality in an otherwise
hygienically designed plant because
poor joints and/or welds will trap
bio-film, thus encouraging bacterial
growth. Bio-film volume increases with
surface roughness, increased tempera-
tures, lower flow speeds and stagnant
areas.
Bio-film formation on inside contact
surfaces of a plant can also exacerbate
local galvanic activity andmicrobiologi-
cally induced corrosion (MIC). Alongside
bio-film, MIC can significantly impact
capital equipment life.
Welding effects include:
• Welding process-related roughness
in the heat affected zone (HAZ).
• Possible sensitisation leading to
roughness and corrosion attack (low
carbon stainless steels overcome
this).