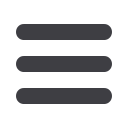

32
AFRICAN FUSION
November 2015
SAIW Member profile: Hydra-Arc
Fexibl CNC cutting solutions
T
he worldwide Koike Group was
founded in 1918 as a family run
business with its head office in
okyo Japan. Today it has global subsid-
iaries across Europe, the US, China and
Korea. “Koikemanufactureshigh-quality
metal cutting, welding and positioning
equipment. We have over 90 years of ex-
perience and serve steel service centres,
heavy equipment manufacturers, gen-
eral fabrication shops, power generation
plants, shipyards, offshore pipe and
vessel fabricators, as well educational
institutes all over the world,” Moriarty
tells
African Fusion
. “The company em-
ploys around 1 200 people globally and
generates revenues of €500-million
every year,” he adds.
“Koike is an OEM manufacturer for
a wide range of CNC cutting machines,
covering all common technologies: la-
ser, plasma, oxy-fuel and water jet. We
also manufacture gas cutting torches,
gas couplings, nozzles in addition an
extensive range of portable cutting and
welding units for straight, bevel, pipe, H-
beamcutting andwelding applications,”
says Moriarty.
Koike have been operating in South
Africa for anumber of years nowthrough
their local distributor Retecon. “Histori-
cally, laser cutting was often preferred
in South Africa, because of the accuracy
and cut quality of laser compared to
conventional air plasma or oxy-fuel cut-
ting systems.”
“With the developments in technol-
ogy, high-definition plasma cut qual-
ity has improved dramatically over the
years, and high-definition plasma cut
parts now meet the required standards
for the majority of steel construction,
engineering and fabrication uses. What
is clear in industry today is a large capi-
tal investment in a laser machine is not
always necessarywhenahigh-definition
plasmamachine, at a third of the invest-
ment cost, is suitable for most jobs.
“However, many factors come into
the equation when one is deciding on a
Thermal cutting:
a new flexibility
The Koike Deltatec 4500 CNC cutting system chosen by Laser Junction. The machine has an effective
cutting area of 3×12 m; a Hypertherm HPR260XD auto gas control, high-definition plasma cutting
system; and two fully automated Koike K-FIT oxy-fuel cutting torches.
African Fusion
talks to Sean Moriarty, South African sales di-
rector for Koike, about the successful implementation of the
company’s state-of-the-art Deltatec plasma/oxy-fuel combina-
tion cutting system installed together with Koike’s machine
distributor Retecon at Durban-based cutting and fabrication
specialist, Laser Junction.
cutting system. We at Koike andRetecon
will gladly advise plus recommend and
offer the right cutting solution for our
customer’s needs,” he adds.
“Each process has its niche in terms
of thickness. Oxy-fuel can be used for
carbon steels on anything from 3.0 mm
all the way to 300 mm plus, while mod-
ern mechanised plasma systems are
most economical and accurate in the
3.0 mm to 40 mm range. Plasma cut-
ting of plate thicknesses above 40 mm
is possible, but at lower quality with
increased consumable costs and gas
consumption. Lasers have their niche for
high-accuracy, high-quality, high-speed
cutting in the 0.8 to 16 mm range, while
water jet cutting, anon-thermal process,
can achieve the highest accuracy and
quality on all types of materials and
thicknesses including woods and plas-
tics – but it is extremely slow compared
to other processes.”
Laser Junction’s new cutting
system
Laser Junction, established in 1995
in Red Hill, Durban, has established
itself as a market leader in the sheet
metal industry, specialising in plasma
cutting, laser cutting, punch bending
and steel fabrication. The company,
one of the largest of its kind in South
Africa, is currently relocating to a new
10 000 m
2
premises at Dube TradePort,
the new Industrial Development Zone
at King Shaka International Airport in
KwaZulu-Natal.
Laser Junction has been a loyal cli-
ent of Retecon for over six years, and,
to meet the need for a cost-effective
cutting solution for thicker sectionmate-