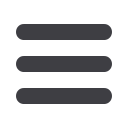

November 2015
AFRICAN FUSION
29
plants
subject to health regulation
Figure 1. An example of an ideal weld, a TIG orbital weld on 316L electro-
polished stainless steel pipe.
Figure 2: An unacceptable manual weld with defects including
lack-of-penetration, misalignment, a crevice, and a poor ID purge.
• Heat induced oxidation in the HAZ
(inert purging gas needs to be used).
• Geometric effects from misalign-
ment and/or uncontrolled welding
of root beads leading to stagnant
regions.
• Cooling of heterogeneous filler
metal leading to micro cracking.
• Pickling and passivating chemical
treatments affecting surface rough-
ness.
• Fit-up effects from poorly cut and/
or aligned pipe-ends leading to local
under or overfill.
Pipe welding
For pipework, the preferred fabrication
method is automatic orbital welding
as this is capable of producing consis-
tently high qualitywelds. Process plants
require a significant level of on-site
assembly welding of small-bore thin-
walled pipes, in particular. Welds on
the product-contact side must be con-
tinuous; they must be smooth enough
to allow proper cleaning.
Figure 1 shows an ideal welded
joint, a TIG orbital weld on 316L electro-
polished stainless steel pipe. Theweld is
fully penetrated with a uniform crevice-
free inner weld bead showing good
pipe-to-pipe alignment. The internal
diameter (ID) was purged with argon.
To achieve this:
• Pipes must be dimensionally
matched (within 20% by weight).
• Alignment, fit-up, orientation and
cleanliness must be controlled.
• Weld procedure used is alignedwith
the sulphur % (Note changes and
effect of changes in 316 composi-
tion limits).
• Tungsten geometry is diamond
ground and correct.
Figure 2 shows a manual weld taken
from an operating pharmaceutical
plant. This unacceptable weld has
defects including lack-of-penetration,
misalignment, a huge crevice, and a
poor ID purge.
Impact of pipemanufacturing
and fabrication
Several factors lead to inadequate
welded joints and pipe fabrication.
One of these is pipe geometry. Pipes
designed to be circular are often oval
due to manufacturer inputs related to
the rolling, slitting, forming, seamweld-
ing and cutting to length operations.
Pipes are manufactured to diameter,
wall thickness and ovality tolerances.
These tolerances affect the matching
and alignment of pipe-ends, which are
otherwise correctly prepared. Whilst this
is a matter beyond welder control, the
fabricator can influence choices. In ad-
dition, fabricator centroidmisalignment
is important.
In the case of thin walled pipes,
the impacts of tolerances on hygienic
fabrication can be significant in terms of
the increasedCIPoperations required to
maintain an acceptable product.
To test the impacts of pipe manu-
facture on weld integrity, 90 × 316L
stainless steel pipes and bends from
the then current Okahandja brewery
project in Namibia were measured by
the fabricator in India. Maximum (major
axis) andminimum(minor axis) external
diameters and three equally spacedwall
thicknesses were tabled. Of these 90
pipes, 27 related to 50 mm ID, 1.5 mm
wall thickness pipes were analysed.
These naturally fell into two distinct
groups, one with tight manufactur-
ing tolerances (ovality 0.04-0.07 mm)
and one with wider tolerances (ovality
0.17‑0.51 mm).
A Monte Carlo-based mathematical
algorithm was developed to assess in-
terconnecting pipes against the criteria
of a point-by-point minimum overlap of
80%around the pipe circumference. (Or-
bital weldingmanufacturers prefer 95%).
The algorithm included three parts: an
external ellipse; an internal shape; and
a randommisalignment. The external el-
lipsewas definedby themeasuredmajor
andminor axes, and the internal surface
by the external ellipse less the local wall
thickness. This was modelled as a ran-
domly orientatedquartic functionbased
on the three wall thicknesses taken for
each specific pipe and themisalignment
by allowing for a random6%variation of
wall thickness (0.1 mm).
Twelve pipe alignment situations
were measured. Each involved 1 000
iterations. The minimum overlap for
each iteration case was recorded onto
a histogram.
The cases included: fitting one
straight, high-tolerance pipe to another
with no orientation control; and fitting
one randomly selected, high-tolerance
pipe to another with major axis align-
ment. The fit-up models were repeated
using low tolerance pipes, and connect-