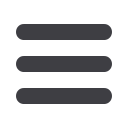

November 2015
AFRICAN FUSION
33
and precision benchmark
Koike’s Katana-ADV CNC controllers
incorporate all of the software for controlling
the cutting path of the torches, along with
the electrical, flame and gas controls for the
cutting process being employed.
The Koike system offers high definition cost-
effective plasma cutting on plate of up to
40 mm, plus the added flexibility and value of
cutting plate of over 150 mm using oxy-fuel.
Laser Junction has established itself as a
market leader in the sheet metal industry,
specialising in plasma cutting, laser cutting,
punch bending and steel fabrication.
rial, decided to complement its fleet of
machinerywith a combined plasma and
oxy-fuel installation.
The Koike Deltatec 4500 CNC cut-
ting system was chosen, a machine
with a 4.5 m beam width on a 14 m rail
length, giving an effective cutting area
of 3×12 m. For cutting, the machine
has one Hypertherm HPR260XD auto
gas control high-definition plasma cut-
ting system, combined with two fully
automated Koike K-FIT oxy-fuel cutting
torches, all under the control of Koike’s
Katana-ADV CNC controller.
“These controllers incorporate all
of the software for controlling the cut-
ting path of the torches, along with the
electrical, flame and gas controls for
the cutting process being employed.
When plasma cutting, for example,
Hypertherm’s True Hole® technology
enables high-quality, bolt-ready holes
in a 1:1 ratio to plate thicknesses of
between 5.0 mm and 25 mm on mild
steel material. This is testament to the
quality, accuracy and process speed of
the Koike machine in combination with
Hypertherm’s XD plasma systems,” Mo-
riarty points out.
He highlights the Portal Frame
Compensation (PFC) system feature.
The saddles of the Deltatec have a built-
in system that enables the gantry to
expand with the heat from the cutting
processes, whilemaintaining a constant
clearance between the rack and pinion
on both sides of the drive system. This
ensures a smoother cut surface and less
wear on the rack and pinion systems.
At start-up, the machine will auto-
matically measure and calibrate the
portal’s squareness using two sensors
– the actual portal position will be
compared with the initial CNC settings
when the machine was assembled. The
Katana controllerwill showanon-screen
message that warns the operator if the
portal is out of spec and readjustment
is required.
Other features Moriarty points out
are the SmartLift torch carriages to-
gether with Smartflow gas distribution,
for both plasma and oxy-fuel, incorpo-
rated in the Deltatec 4500. The plasma
torch, which requires very accurate
height control for high definition cut-
ting accuracy, is fitted with a magnetic
torch holder for collision protection and
maintenance-free ac slide motor with a
precision linear guidance system. The
oxy-fuel torcheswithheat protectionuse
electronically controlled proportional
valves with capacitive height sensing
including an automatic pre-heat and
ignition system. In addition:
• A spot laser pointer enables easy
manual plate alignment and refer-
encing between cuts.
• An E-cabinet air conditioning sys-
tem maintains the temperature
of the control cabinet at the ideal
operating temperature in ambient
temperatures ranging from -10 °C
to +55 °C.
• A voltage stabiliser compensates for
fluctuation of between +10% and
-30% from 230 V.
• A network cable connects the Kata-
na controller to a local area network
(LAN). “Should any faults developon
the Laser Junction’smachine, Koike
Europe can log in via Team Viewer,
diagnose the fault conditionand talk
local technicians through a resolu-
tion procedure,” Moriarty explains.
Also supplied with the turnkey installa-
tion at Laser Junction is the SigmaNest
nesting software, which was originally
developed in South Africa by Mecad
Systems. This allows optimisation of
material usage and productivity. “While
the software is globally supported, be-
cause of the local expertise in this area,
Laser Junction’s SigmaNest systemwill
be directly supported byMecad in South
Africa,” Moriarty says.
The cutting table itself is aHerr Plas-
Vent exhaust-type table with a modular
construction. Exhaust channels run in
the longitudinal direction in separate
515 mm transverse sections. “Each of
the channels has an exhaust flap, which
is automatically openedwhen cutting in
that section. This enables fume extrac-
tion in the areaswhere it is needed,mak-
ing the extraction processmore efficient
and reducing the fan power required.
“For Laser Junction, this cutting
system significantly extends the com-
pany’s cutting capability. As well as
laser services on plate thicknesses up
to 20 mm, the Koike system offers high
definition, cost-effective plasma cutting
on plate of up to 40 mm, plus the added
flexibility and value of cutting plate of
over 150 mm using oxy-fuel,” Moriarty
confirms.
“In addition, the company benefits
from local service and support from
Retecon and from Koike in Holland, the
OEM of the system. Koike are cutting
specialists. The solutions they offer
are not limited to a single technology
and combination system such as Laser
Junction’s Deltatec plasma/oxy-fuel
system, are not only cost effective, they
can significantly enhance a company’s
offering, while optimising productivity,”
Moriarty concludes.