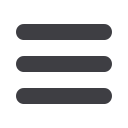

FIGURE 3: Rugged features on insulators which increase the ruggedness of the connector
FIGURE 1:
Multi-finger,
heat-treated
BeCu contact
for high cycle
applications
FIGURE 2:
Phosphor
bronze
contact
designed
for rugged
applications
of contact, usually three to four
“fingers.” (FIGURE 1: Multi-finger,
heat-treated BeCu contact for high
cycle applications)
At the other end of the spectrum,
some interconnect systems have
a relatively stress-free life with
few cycles, possibly in an office
environment. A single beam contact
system is usually sufficient for these
types of applications, and if it is made
of phosphor bronze or beryllium
copper, it will usually withstand up to
100 cycles.
A third contact option is one
designed for high-retention, or
“rugged” applications. The geometry
of the contact beams increase the
normal force and withdrawal force
of the mating terminal. Long beams
and therefore extended insertion
depth make it rugged. (FIGURE 2:
Phosphor bronze contact designed
for rugged applications.)
While the focus of this article is
contact design, we would be remiss
if we did not mention insulator
design in any discussion of rugged
interconnect applications. Plastic
insulator design features that are
useful in environments requiring
rugged connectors include:
•
Board locks on connectors
that mechanically lock two together
two printed circuit boards.
•
Positive latching systems
on discrete wire and IDC cable
systems. Manually activated latches
can increase unmating force by up to
200%.
•
Screw downs which secure
the connector mechanically to the
board.
•
Weld tabs, which significantly
58 l New-Tech Magazine Europe