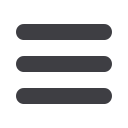

increase shear resistance of the
connector to the PCB
(FIGURE 3: Rugged features
on insulators which increase the
ruggedness of the connector)
PLATING:
Plating is another critical
design factor that determines the
success of the interconnect system.
The best plating finish is whatever
material meets your requirements at
the lowest cost.
Gold is generally specified for high
reliability or low voltage and current
applications. Even in very hostile
environments, it will remain free of
oxides which could cause an increase
in contact resistance. Gold is also
used for contacts that will see a large
number of cycles because excellent
electrical connection can be made
with minimum contact pressure.
Gold is a significant cost adder to most
interconnect systems. Of course gold
is susceptible to price fluctuations.
The impact of the price of gold on
a connector has been alleviated with
the adaptation of using less gold in
non-critical applications. Originally,
Bellcore specifications required 50 µ
inches of gold plating over nickel, for
applications including leads, cables,
and grounding points.
In a bid to remain competitive but still
employ the advantages of gold, many
companies lowered their minimum
gold plating thicknesses to 30 µ or 10
µ inches, or even flash gold.
Tin is a low-cost alternative to gold
plating. It has good conductivity
and solderability, but forms an oxide
coating which must be penetrated
for electrical connection. It is also
susceptible to a form of corrosion
known as fretting. Tin is used in
connector systems where fewer
cycles are expected, or where the
contact can be designed to apply
high normal forces which will cause
sufficient sliding (i.e., wiping action)
during lead insertion, to break the tin
oxide surface film.
The wear caused by this wiping
action is one factor that limits tin
plated contacts to fewer cycles than
gold. It also requires an increased
plating thickness, often 150 µ inches.
While economics are an important
consideration, the requirements of
a particular product are more likely
to dictate which plating is used.
Selective gold/tin plating is a popular
plating option because it provides
designers with the best of both
worlds. The critical contact area has
the reliability of gold, and the tail has
the lower cost and solderability of tin.
New-Tech Magazine Europe l 59