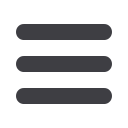

Technology News
www.read-tpt.com54
M
arch
2015
Tube industry solutions
THE year 2014 was positive for Adda
Fer Meccanica, which increased its
global presence and confirmed itself as
a solid and reliable partner, not only for
the study and the realisation of individual
plants, but also as a partner able to
provide turnkey solutions, complete and
integrated, for the production of high
quality steel pipes.
The group reached a turnover of
more than €20m and the year 2015
started with renewed confidence and
optimism about the challenges which
are waiting for the company thanks
to the a number of exciting
projects: No. 7 Cutting Line
DB10 double blade shear
for one of the largest tube
manufacturers in the world,
that will be installed in Texas,
USA, in the first months of
the year; packaging machine
for tubes up to 5" in the
USA; TM4 tube mill for the
production of tubes up to 4"
in Europe; TM3 tube mill for
the production of tubes up to
3" with packaging system in
Africa; and a tube finishing
line and an automatic packaging
system for pipes up to 8" in Vietnam.
Recently Adda Fer Meccanica
supplied a complete line for the
production of electro-welded pipes up to
219.1mm (8") diameter to an important
Vietnamese pipe manufacturer.
The new tube mill is able to produce
round tubes from 76mm to 219.1mm
diameter, square tubes from 70mm
x 70mm to 175mm x 175mm and
rectangular tubes from 100 x 40mm to
200 x 150mm.
Range thickness is from 3mm to 8mm
while the length range is from 6m to
12m. The maximum working speed is
about 60 mt/min.
Meccanica Adda Fer Srl
– Italy
Fax: +39 035 494 6564
Email:
info@addafer.itWebsite:
www.addafer.itAdda Fer had a successful 2014
Increase in pipe-cutting reliability
with new split-frame technology
ENERGY sector portable machine
tool specialist Mirage Machines, an
Acteon Company, has achieved a step-
change in the operational efficiency
and reliability of cutting technologies
for pipeline and plant fabrication
manufacturers and contractors in the
international energy sector.
Rising fabrication and maintenance
project activity, including works
on wellhead, riser and caisson
assemblies, has significantly increased
demand from construction yards,
operators and dutyholders for new
pipecutting technologies across the
Americas, EMEA and Asia-Pacific.
UK-based manufacturer and supplier
Mirage Machines has evolved split-
frame machine technology with the
development of its MSF (Mirage Split-
Frame) machine, which significantly
improves the efficiency of pipecutting
operations on infrastructure composed
of heat-resistant, stainless and super-
duplex metals.
Mirage has developed innovative
new self-squaring capability for the
fully-portable MSF, reducing the risk
of installation error during operations
and significantly shortening the setup
process, maximising the operational
run-time of its equipment.
Richard Silk, managing director
of Mirage Machines, says the MSF
technology has applications in every
energy-producing region, and is already
being shipped worldwide to meet rising
demand generated by capex and opex
projects in new and existing oil and gas
infrastructure.
“The pipecutting marketplace is a
significant slice of the portable machine
tool supply chain, yet until now the
technology has not moved forward. The
majority of machines in use have been
based on an operational design which
hasn’t evolved in 30 years,” he said.
“We designed the MSF to bring about
the step change the industry needs
– reducing the weight of the machine
while improving its technical capability,
giving operators and service companies
a more reliable, durable pipecutting
tool which delivers excellent accuracy,
without interruption, at any scale.
“Due to the level of global demand,
we have already increased our
manufacturing capability at our
headquarters in the UK to deliver
work-ready MSF machines across the
regions, and have focussed on being
able to supply from stock in the US
and Australian markets to ensure that
Mirage customers can respond quickly
to the industry’s needs.”
Mirage Machines designs and
manufactures technologies for appli-
cations including drilling and tapping,
flange facing, hot tapping and line
stopping, line boring, milling and gantry
milling, orbital milling; and pipe and
casing cutting.
Mirage Machines
– UK
Website:
www.miragemachines.comThe MSF
technology
from Mirage
Machines