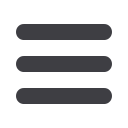

28
Tube Products International July 2015
www.read-tpi.comproducts & developments
Low-force fusion
Thermoplastic pipe fusion equipment
expert McElroy has launched the
Acrobat™ 160, a low-force fusion
machine for 63 to 160mm polypropylene
pipe.
The Acrobat 160 allows operators to
fuse pipe for plumbing, mechanical and
geothermal projects and a variety of
other indoor applications where work
spaces are often very limited. Its small
footprint and light weight makes it an
easy machine to manipulate when
performing fusions overhead as well
as on the ground, within crawl spaces,
attics and other confines.
“The unique installation challenges
that commercial buildings present
was a perfect fit for us because of
McElroy’s extensive background in
product innovation,” said Chip McElroy,
president and CEO of McElroy.
“We are excited to offer job site solutions
in this market with the Acrobat 160 and
our entire line of polypropylene tools
and accessories.”
The Acrobat 160 can be configured from
four to three jaws without using tools,
for added flexibility in tight spaces. The
machine weighs 40lb in the four-jaw
configuration, and only 29lb in its three-
jaw set-up.
The narrow jaws allow fusions for
flanges to outlet branches of tees and
most fittings.
The machine is provided with a
hydraulic power unit (HPU) and inserts
for commonly butt-fused polypropylene
pipe sizes.
The facer and heater can be loaded
from the top or bottom (in the three-jaw
configuration) of the carriage, giving the
operator better access and flexibility
regardless of the joining challenge.
The Acrobat 160 is compatible with
the DataLogger
®
quality assurance
tool, which allows operators to record
and document the key parameters of
the pipe fusion process to ensure the
integrity of fusion joints and increase job
site accountability.
It is also available in a productivity
package that includes a manual machine
stand and two PolyPorters
®
, which aid
in lifting the pipe as well as performing
as a pipe stand.
McElroy
– USA
fusion@mcelroy.com www.mcelroy.comMcElroy’s Acrobat 160 low-force fusion machine
DP Seals sets NORSOK standard
Seal and moulding manufacturer
DP Seals is setting a standard in
components conforming to the rigorous
NORSOK M-710 benchmark, and
claims to be one of the few companies
to insist on only using materials that
meet the full requirements of just the
top two grades.
Originally developed by the
Norwegian petroleum industry, M-710
has now become an internationally
recognised standard for non-metallic
seals and bearings, offering oil and
gas companies an assurance of
quality, performance and durability
in components designed to operate
in hostile sub-sea environments. To
meet M-710, materials must achieve
accepted criteria for both rapid gas
decompression (RGD), also known
as explosive decompression (ED),
and sour gas ageing (H
2
S), both of
which are proven indicators of long-
term performance and viable life
expectancy.
DP Seals has been working to the
NORSOK standard virtually from its
inception, and has developed and
supplied a wide range of seals and
custom-moulded components to
customers in the UK, Scandinavia and
further afield.
“High quality components have been
the cornerstone of our success,” said
MD Andrew Piper, “and adhering to
M-710 is simply one more way in which
we can be sure of meeting the stringent
specifications of our customers in the
oil and gas industries.”
A stand-alone website (www.
norsokready.com)has been launched,
with full information on NORSOK
testing criteria and a list of approved
materials used by DP Seals.
DP Seals Ltd
– UK
sales@dpseals.com www.dpseals.com