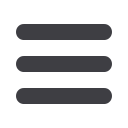

July 2015 Tube Products International
33
products & developments
Oswal expands into USA, Europe and Japan
Industrial valve manufacturer Oswal
Group has experienced robust growth
in recent years. Starting with a foundry
in Gujarat, India, in 1985, the company
ventured into industrial valves in 1995.
The products and services offered
serve all markets and industrial sectors.
With a full complement of engineering
resources and facilities Oswal Infra
provides process equipment and
process skids with complete automation
for both domestic and international
markets. Products and services include
process equipment, pressure vessels,
heat exchangers, tanks, columns,
process skids and process packages.
Export sales have grown by more than
50 per cent in the last two years, and
the company has seen a large increase
in orders for higher alloys such as
Duplex, Super Duplex and exotic alloys,
and cryogenic and critical application
valves. To further expand its presence
in the global market, the company has
opened offices in Europe, the USA
and Japan, having already established
itself in the Middle East. Valves and
skids manufactured by Oswal Group
are primarily used in oil and gas,
petrochemicals, refineries, power,
steel, chemicals and fertilisers, water
treatment, offshore, nuclear and other
sectors, in India and around the world.
Oswal Industries Ltd
– India
mktg@oswalvalves.com www.oswalvalves.comTube connection breakthrough speeds
assembly of instrumentation systems
A breakthrough in high-integrity
tube connection technology that
offers performance and time-saving
advantages to instrumentation system
designers and installers is now available
from Parker Hannifin.
Designed for working pressures as high
as 22,500 psi (1,550 bar), the new
‘flared cone’ technology advances the
performance of compression style tube
connections. It provides users with a
simple and reliable means of speeding
the assembly of instrument tubing
systems for use in higher pressure
applications in the oil and gas industries.
Developed by Parker Autoclave
Engineers, the new flared cone
connection (FCC) technology is an
advance on the type of ‘cone and
thread’ tube connections pioneered by
the company.
The new connections are simpler to
make up, and installers can typically
complete the task in less than four
minutes, after only minimal training.
Flared cone connections are also
effective in applications where leaks
caused by vibration are an issue.
According to Michael O’Keane,
product marketing manager for Parker
Autoclave Engineers, “Our new FCC
technology offers the best of both
worlds. It combines the make-up and
installation simplicity of compression-
style connections with the strength of
cone and thread, and has more features
and higher pressure capabilities than
similar technologies.”
The patent-pending FCC technology is
based on a single sleeve compression
style system. However, unlike conven-
tional designs, the tube end is flared to
prevent any possibility of ejection, and
also provides the connection’s primary
metal-to-metal seal. When the gland
nut is tightened, the inside surface of
the anti-ejection flare mates with a cone
in the fitting or valve. The compression
sleeve then mates with the body of
the component to form a second,
redundant, metal-to-metal seal.
This dual seal approach has a major
reliability benefit: in the unlikely
event that the primary seal fails, the
secondary seal preserves the integrity
of the connection. Installing a flared
cone connection is simply a matter of
screwing the gland nut into the fitting or
valve and tightening it to the prescribed
torque.
Parker Hannifin
– UK
ipd@parker.com www.parker.com/ipdThe new tube connection technology uses a flared cone design that
prevents tube ejection and forms the primary metal-to-metal seal
Flared cone connection technology is designed
for working pressures as high as 22,500 psi