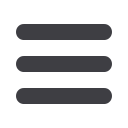

46
Tube Products International July 2015
www.read-tpi.comproducts & developments
Pushing the limits of EDM inspection
Scan Systems, a USA-based company
in the OCTG industry, offers “out-of-
the-box” on-location custom flaws
and artificial reference indicators to
create test standards for calibration.
The company has developed innovative
detection technology over the years that
has helped to overcome a number of
challenging industry obstacles.
EMI inspection machines have
traditionally relied upon slip rings to
transmit data from the longitudinal
rotating assembly back to the computer
for processing and interpretation. Worn
out or dirty slip rings can cause signal
loss, leading to less reliable data and
unseen indication of potential flaws.
Scan Systems applied some Silicon
Valley-style technology to the EMI
process and has incorporated wireless
capabilities into its M-Series EMI
inspection equipment, and removed
slip rings from data transmission. This
development utilises a Wi-Fi radio inside
a rotating head spinning up to 250rpm,
and overcomes the large amount of
magnetic flux created by the surrounding
large electromagnets. This benchmark
in the industry allows for improved data
accuracy and elimination of significant
data errors, and because the data is
digitised immediately at the sensor, any
signal noise from outside interference
is non-existent. “Your Internet went
wireless years ago. It’s about time that
EMI inspection equipment followed
suit,” said Matt Rutledge, general
manager/VP of Scan Systems.
Scan Systems’ ESP upgrade to its
M-Series line is the first EMI inspection
technology to use hall elements in the
longitudinal sensors, which enable
detection and repeatability on flaws up
to 30° off the axis on the OD surface
and 20° off axis ID surface (industry
standard is 7° to 10° off axis).
Additionally, by utilising hall elements,
the number of sensors can increase
from 16 to 64 channels of data for
better resolution and ability to detect
much smaller flaws than the limitations
of traditional PC coils. Scan Systems
claims to be the first in the world to
bring the ability to detect oblique flaws
to EMI inspection. Also, because of the
use of hall elements and the proprietary
Digi-Pro
®
processing software, if the
operator is set to detect at 30°, he
will pick up flaws between 0° and 30°,
making for a more accurate and precise
pass.
Scan Systems has developed an
EMI system that can report the linear
location of a longitudinal flaw, the
circumferential location, and whether it
is on the ID or OD surface of the pipe.
Historically, EMI inspection equipment
was limited to reporting the linear
location of a potential flaw. Though a
few manufacturers would discriminate
between ID and OD indications, the
reliability of the methods utilised made
the reporting less than accurate. Through
significant innovations made in sensor
technology, data collection methods
and sophisticated software algorithms,
Scan Systems’ latest ESP upgrade to
the Pitco™ M-Series EMI inspection
now provides the inspector with a level
of accuracy unseen in EMI inspection
of OCTG material. This advancement
provides the circumferential location
and can report on multiple flaws on
the same plane and ID/OD location in
degrees of probability, saving valuable
time during the prove-up process.
One of the toughest tasks for an EMI
unit operator can be interpreting and
locating the signal from a pipe flaw.
Having an alternative view of the data
can be beneficial in determining a pipe’s
condition. Scan Systems developed a
display that not only makes it easy to
illustrate where pipe flaws are located
but also provides additional information
on the characteristics of the flaw.
Many OCTG MFL equipment manu-
facturers claim their machines detect
flaws on 0.545" (13.84mm) walls and
greater during the inspection process,
but often these claims ignore a key
component of a quality inspection –
repeatability.
This refers to equipment’s hardware and
software capabilities to identify the signal
given by an imperfection or artificial
reference indicator and report those
imperfections at a similar amplitude
consistently and repeatedly.
API 5CT specifications require a
minimum of 20 per cent repeatability
on all inspection runs. Using advanced
signal processing algorithms combined
with proprietary sensors and cutting-
edge signal detection hardware, Scan
Systems’ Pitco M-Series with ESP
upgrade has dramatically improved the
ability to separate a flaw’s signal from the
background noise offering the best S:N
ratio on any given pipe. Scan Systems’
Pitco M-Series with ESP upgrade can
reliably detect and repeat on N5 ID
notches up to 0.545" (13.84mm) wall
thickness and N10 ID notches up to
0.625" (15.875mm) walls.
Scan Systems Corp
– USA
mattr@scansystems.com www.scansystems.comThe Pitco M-Series from Scan Systems