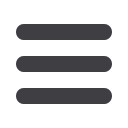

Technology News
www.read-tpt.comJ
anuary
2016
33
Clean room in operation
at Sikora AG
THE Purity Scanner laboratory and
developing area at Sikora was extended
with a new clean room in 2015. Due
to the constantly filtered air and the
slight overpressure in the room, plastic
materials can be tested for impurities
under clean room conditions.
This provides the perfect conditions
for reliable detection and sorting results
by the Purity Scanner. “Thanks to the
implementation of the clean room,
we are able to work with the smallest
probability of external contamination and
achieve the best possible test results,”
said Klaus Bremer, project manager for
the Purity Scanner.
The new clean room for the Purity
Scanner was positively tested and
perceived by many customers. Further
material tests are also planned in
Bremen and can still be requested
on short term. When purchasing the
device, charges for material tests are
refundable.
Sikora AG
– Germany
Email:
sales@sikora.netWebsite:
www.sikora.netKlaus Bremer, project manager, Purity Scanner
Orbital tube processing
equipment
AXXAIR manufactures and sells
a complete range of orbital tube
processing equipment, from cutting,
facing and bevelling to orbital welding
machines. Its research and development
department is continuously developing
the products and adding innovations
to improve customers’ productivity and
satisfaction.
Axxair has therefore revisited the
complete range of orbital open heads,
launching a new smaller model, the
SATO-40 with water cooling and wire.
This model is necessary whenever the
package around the tube is tight and the
access difficult.
The other models, SATO-80, SATO-
115, SATO-170 and SATO-220, have
been improved with a more compact
design, for a lighter machine with an
ergonomic approach. They all have
mechanical tracking through a tracking
ring which avoids marking the outside
shape of the tube. The wire fixing has
also been improved in order to follow
the main hosing and therefore keep a
lower package.
All these models can be upgraded
with the AVC/OSC/WIRE module,
allowing the user to weld thicker pipes
up to 12.7mm (½") thickness.
All the models can be equipped with
an angular head drive to better adapt to
the working environment.
Powered with a range of orbital
welding power sources, these machines
are suited to helping
increase
productivity
through simple and
easy operation. The
auto-calculation function
adapts the parameters,
from diameter, thick-
ness and material to
configuration information.
The colour touchscreens
display the main functions
very simply and intuitively
in order to have a very
quick learning process.
The closed head
range is also growing.
The new models include
the SATF-40MI, SATF-
65MI and SATF-115MI. These heads
are directly compatible with all AMI
power sources that are equipped with
auto calibration.
The facing range is completed with
two new models. DC115-AM2 is a collet
system facing machine driven by a
Metabo motor. This model allows similar
tool adjustment to the smaller model
DC65. It can be equipped with two tool
holders and is suitable for customers that
want a real burr-free square cut in semi-
conductor industries and pharmaceutical
industries on electro polished tubes.
The model DC115-BM2 is a concentric
clamping facer that allows the clamping
of a wide range of tubes to be faced
without having to buy one collet per
diameter, and is claimed to be unique
in the market. It can clamp from 12mm
to 115mm. It can also be equipped with
two tool holders to allow facing and edge
bevelling on tubes. This model is for the
workshop as it cannot be lifted on the
tubes. This model will be completed soon
with a DC221, which will allow the facing
of tubes up to 220mm.
Through subsidiaries and a network of
distributors Axxair can serve customers
in more than 60 countries around the
world and offers a global approach from
prepping to automatic orbital welding on
tubing and piping.
Axxair
– France
Website:
www.axxair.com